Je cherchais un projet pour apprendre à souder à l’arc. J’avais vaguement appris les rudiments, et de nombreuses fois, le poste et la technique m’ont manqués pour aboutir des créations diverses. Cette idée dans un coin de ma tête et quelques photos de cyclekart ont fini par me décider. J’allais me lancer dans la construction d’une caisse à savon: ces petites voitures d’enfant, en général à pédale. Et c’est là que c’est parti dans tous les sens …
En pleine flambée de popularité du vélo électrique, mini moto, kart électriques, beaucoup de composants (moteurs, batteries, électronique de contrôle) sont devenus très abordables et autorisaient une version motorisée. Je pars donc sur une voiture électrique pour enfant de 5-10 ans !
Le châssis
J’opte pour du tube acier 20x20mm pour toute la structure. Pour un châssis d’à peine plus d’un mètre, un enfant tient debout sur une barre sans la plier. Dimensionnement validé ! Pour mes soudures, je n’arrive pas à découper proprement à 45°. Donc je fais des découpes bizarres sur un tube pour ne laisser qu’une face sur laquelle vient s’appuyer le deuxième tube à angle droit. Je soude le tout à plat. Je procède à la tige de 1.6mm et progresse par points successifs le long de ma découpe. J’abandonnerais vite cette méthode car elle demande trop de temps de découpe. Mais voici le premier cadre réalisé de cette manière.
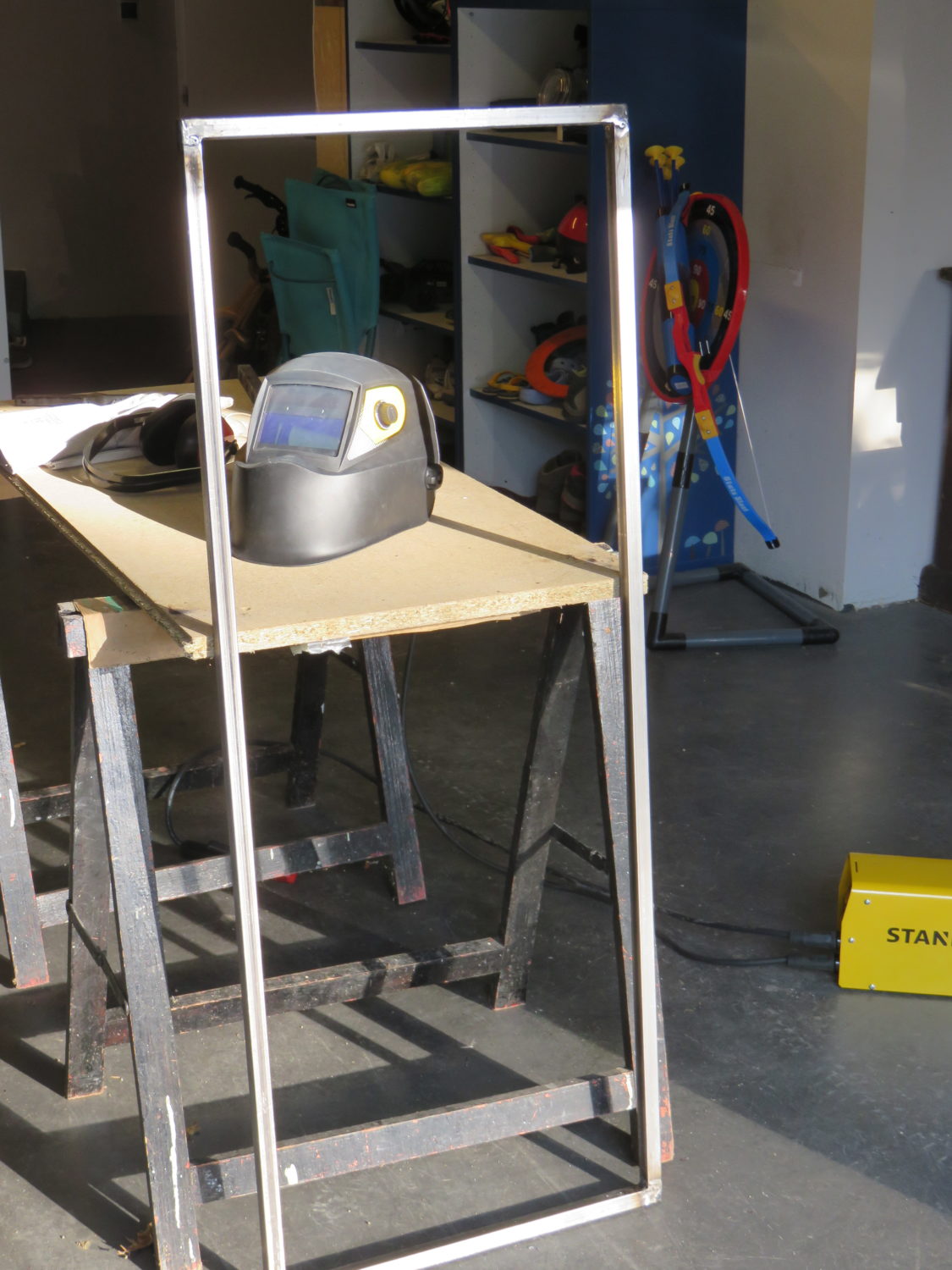
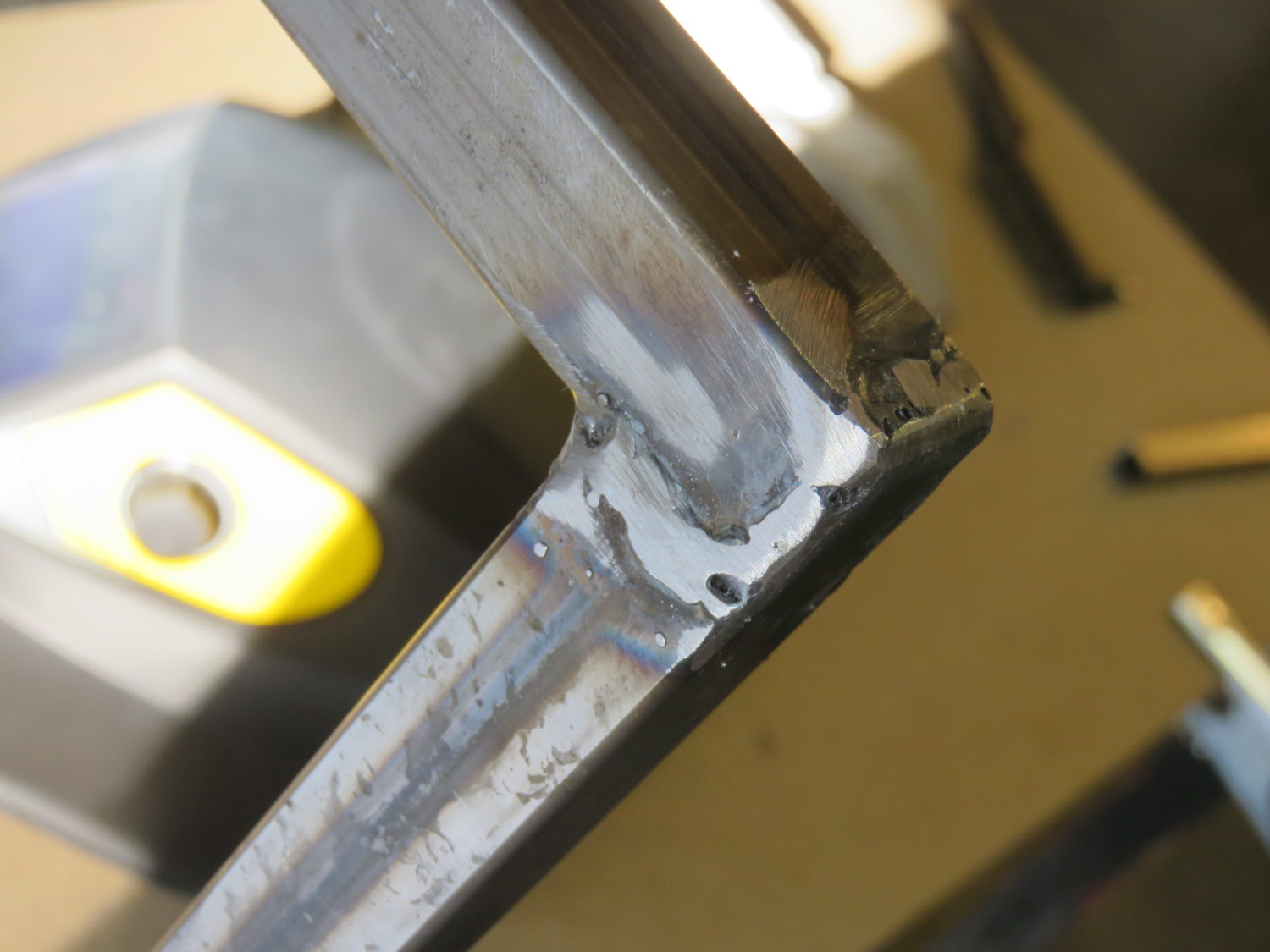
J’ai les dimensions principales calées pour faire rentrer un enfant assis, et rentrer le cyclekart dans ma remorque. Donc je fixe les principaux éléments dimensionnant. L’essieu arrière. Je choisis un tube acier plein de 12mm et achète deux paliers: des roulements dans des cages de fontes permettant de les fixer. Mais j’abandonne l’idée de boulonner pour ne pas fragiliser mes tubes aciers du châssis par des perçages: je soude ! Soudure fonte/acier à l’électrode pour acier … pas facile alors je fais tout chauffer au rouge côté fonte pour assurer la soudure. La graisse de mes roulements chauffe et s’enflamme pendant que je soude ! Pas facile, c’est pas joli, mais ça tient…
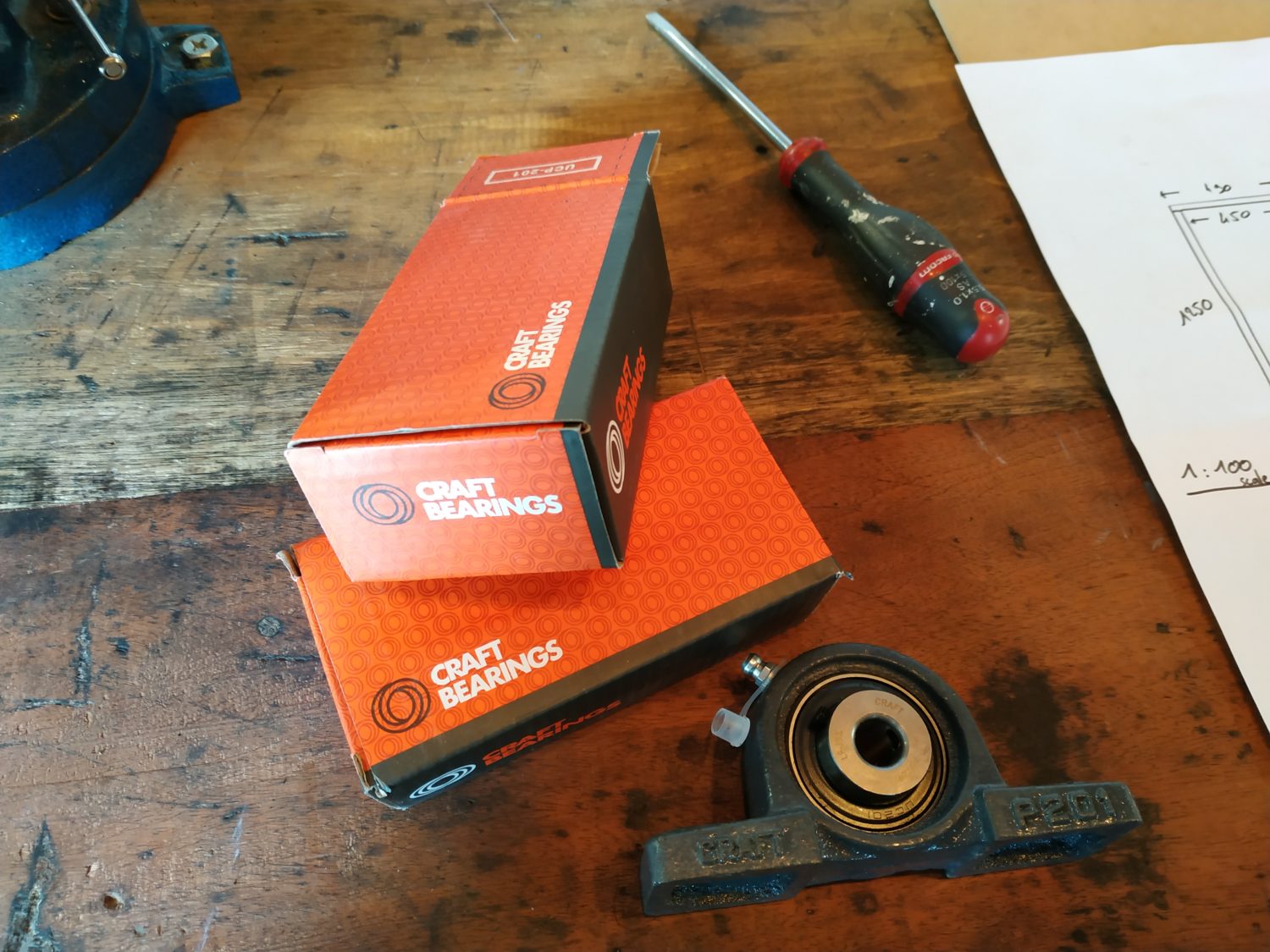
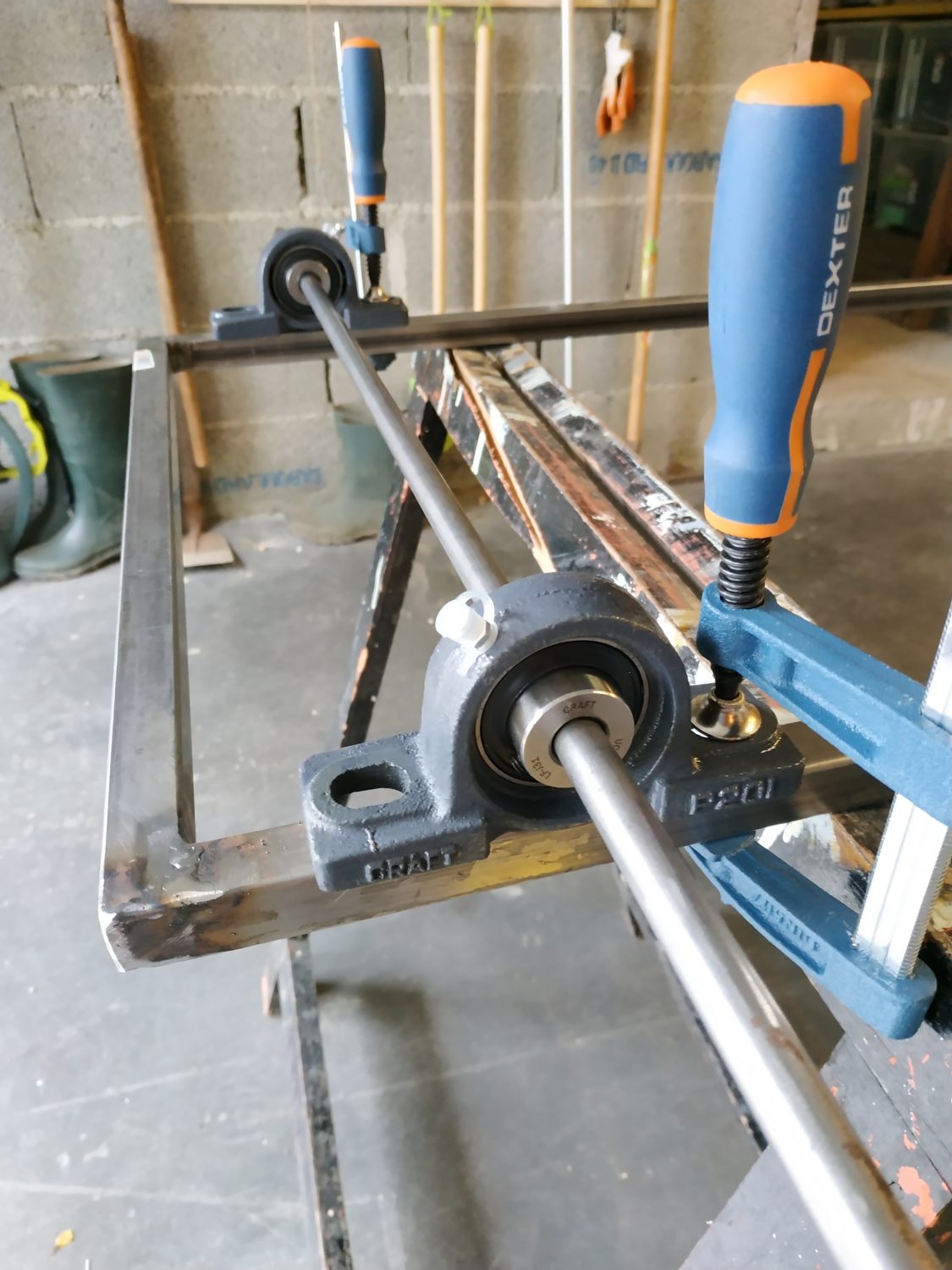
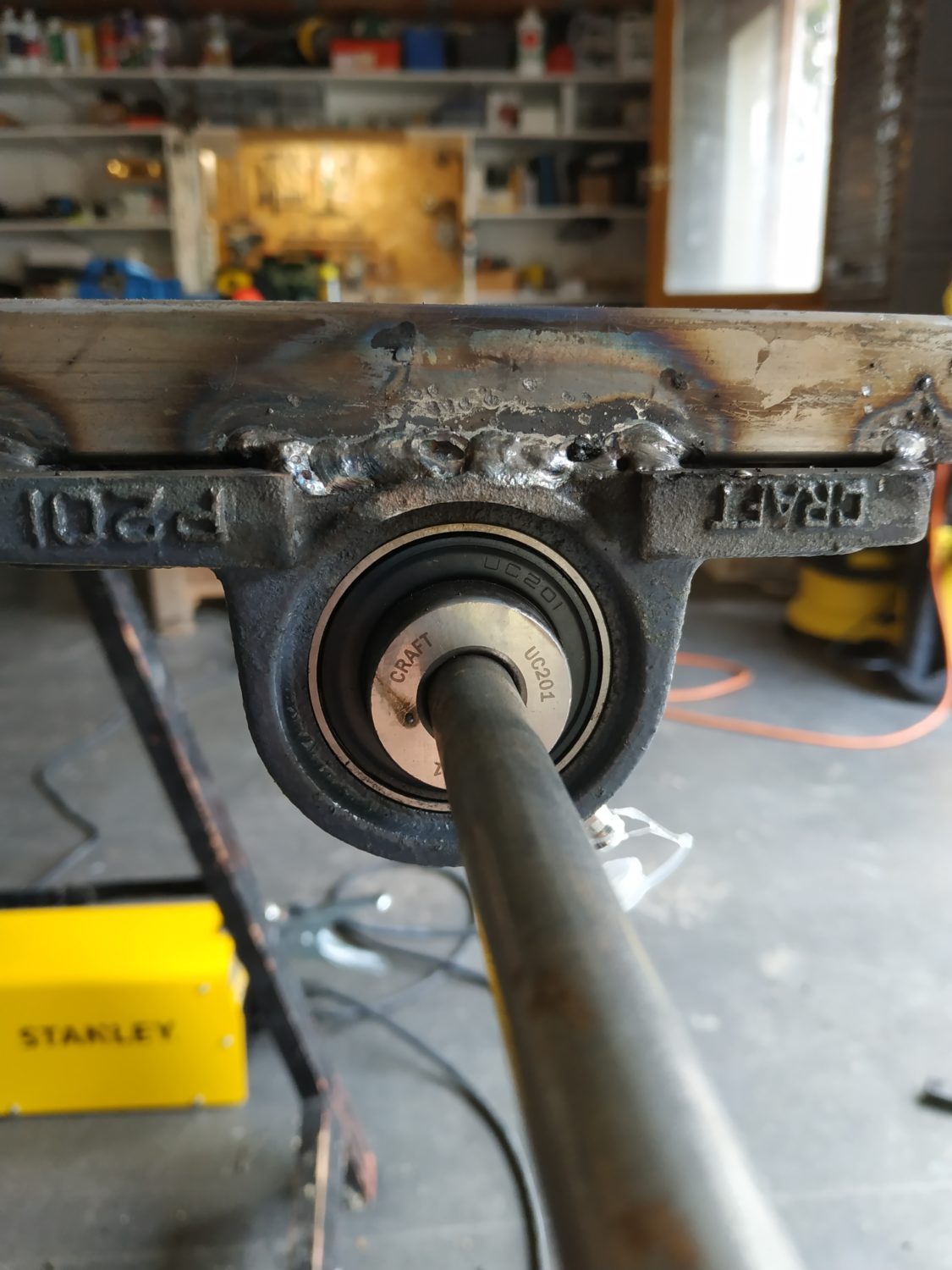
Les roues avant
Après l’essieu pour les roues arrières, je m’occupe des roues avant. Elles doivent assurer la direction, et donc pivoter librement. Je dois donc éloigner la roue du cadre du châssis et assurer sa rotation selon un angle suffisant. Je crée donc cette pièce qui viendra prendre en sandwich mon châssis et permettra de fixer une roue à son extrémité. L’important est de bien anticiper l’écartement entre les deux fers plats, qui doit être égal à l’épaisseur du tube du châssis + l’épaisseur des roulements qui permettront une rotation libre.
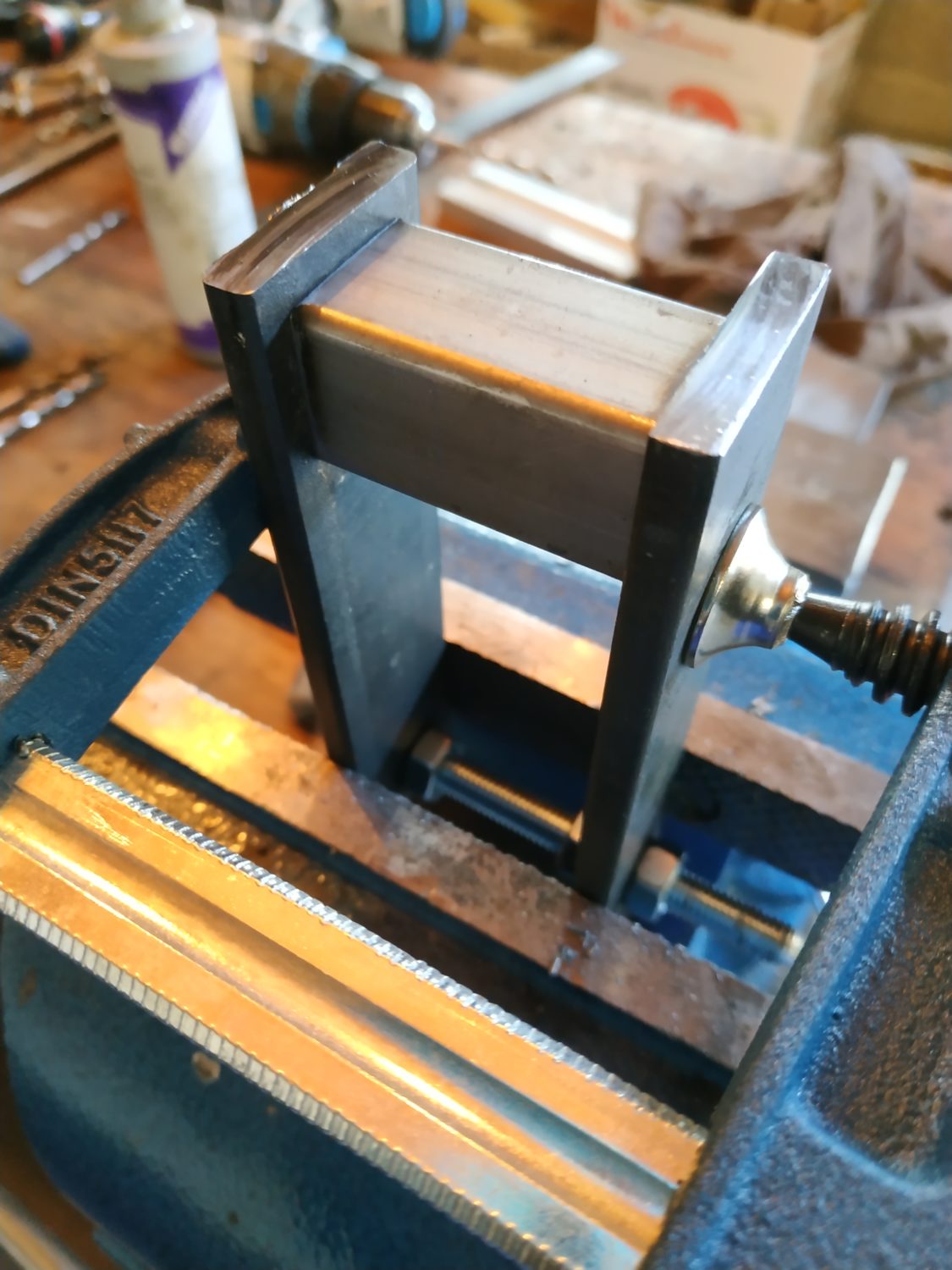
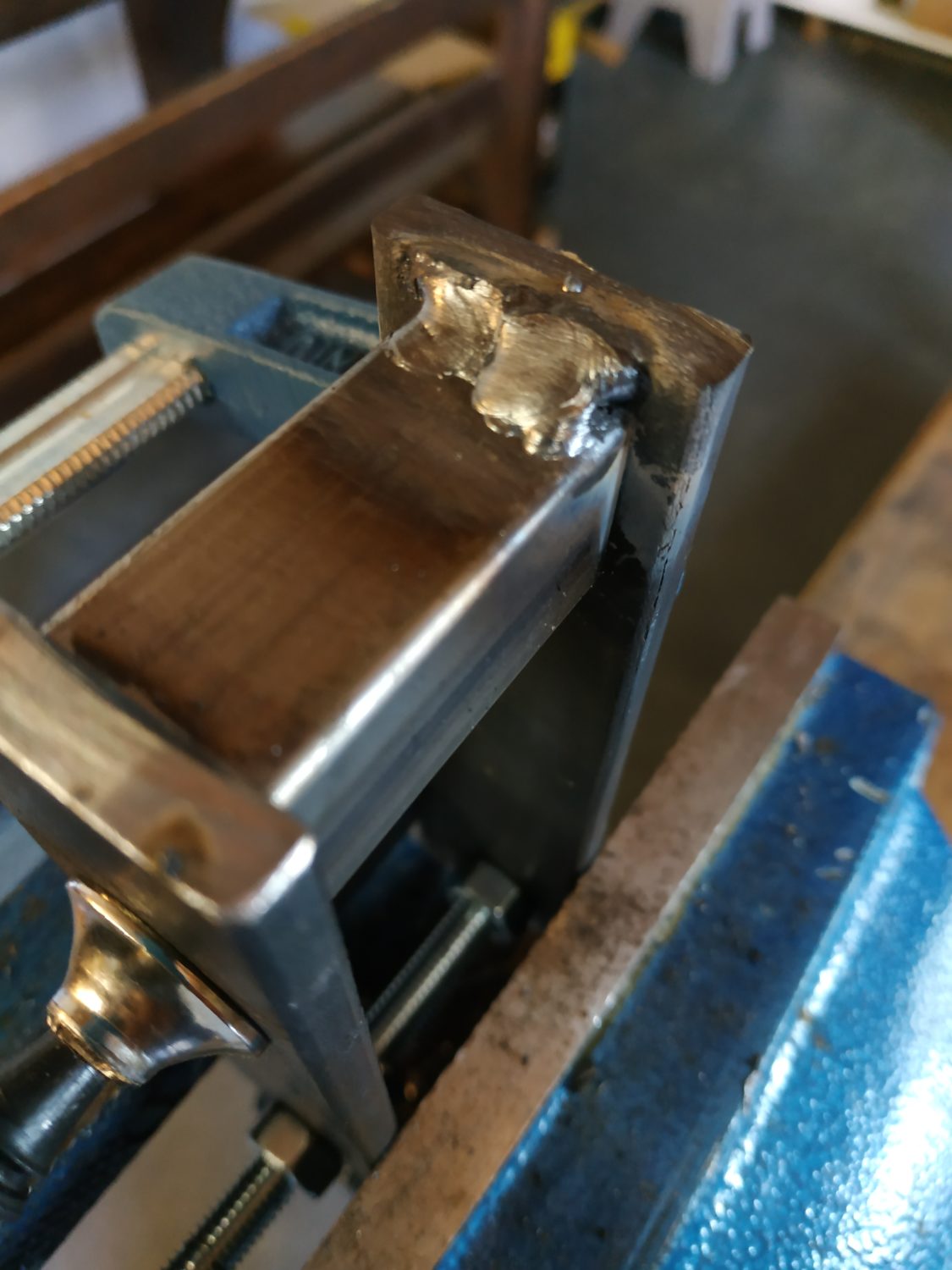
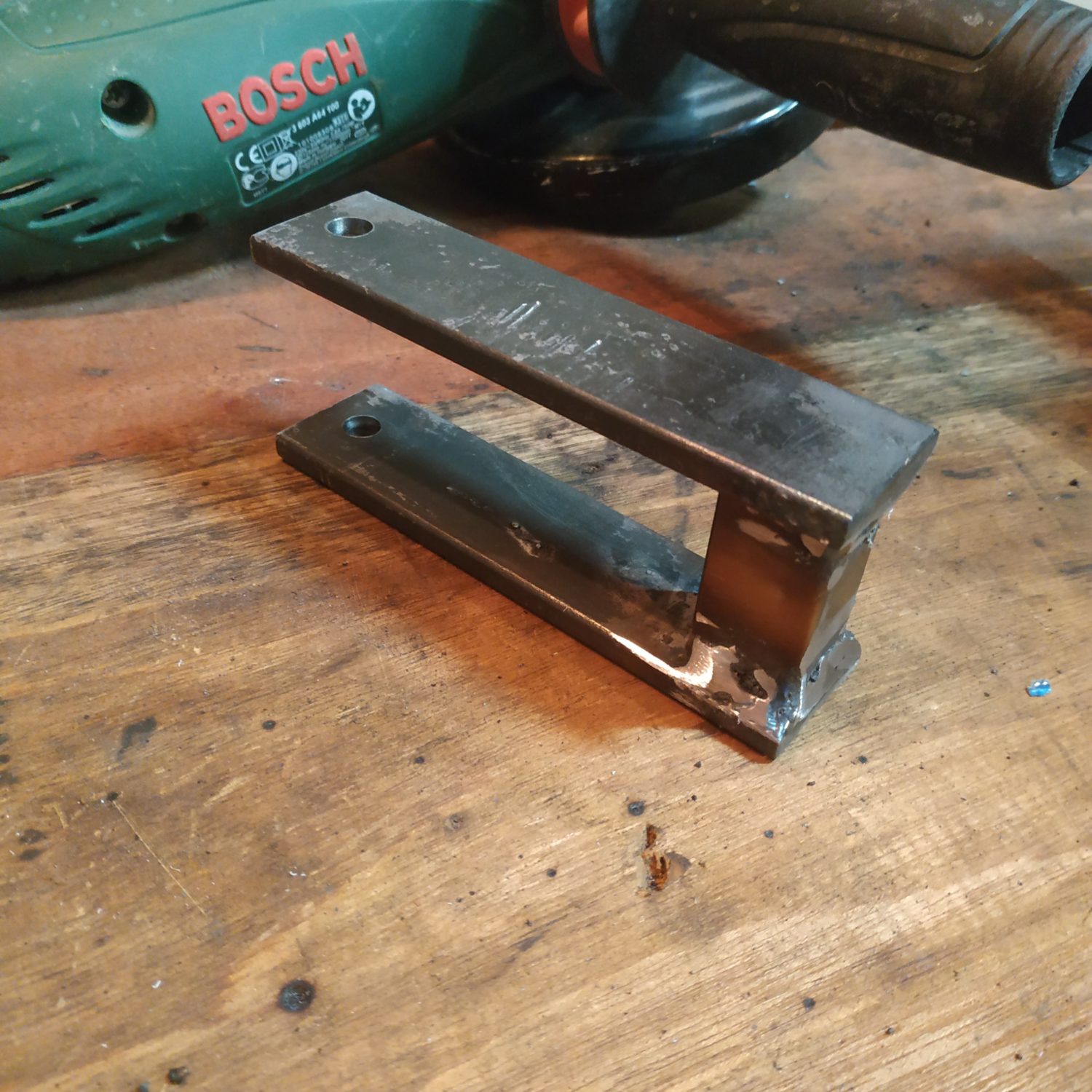
Je fais en sorte d’avoir le trou le plus petit possible pour ne pas fragiliser les tubes du châssis. Plus petit que le diamètre central de mes roulements, cela m’oblige à bricoler des entretoises qui permettront au roulement de rester centrer sur l’axe de rotation: j’use un écrou en le faisant tourner sur la perceuse avec la meuleuse dans l’autre main … Je peux maintenant monter les deux roues avant et régler finement le serrage des roulements pour que ça coulisse sans jeu et sans forcer grâce à des écrou avec frein filet (le plastique bleu dans l’écrou qui empêche les dévissages intempestifs. La roue est maintenue sur un seul côté de son axe, une tige filetée pleine de 12mm. Ca supporte mon poids sans faillir, je valide donc ce montage.
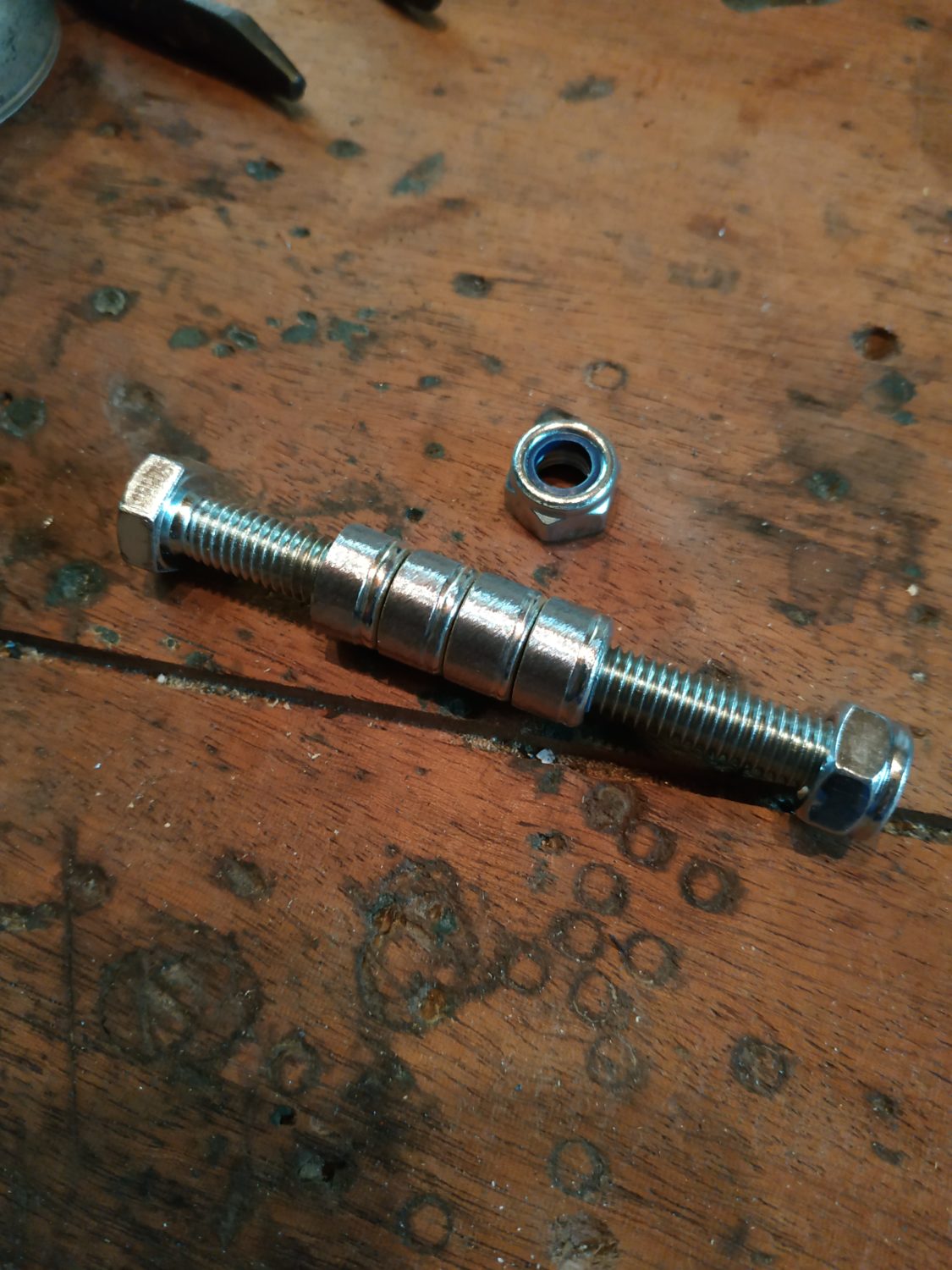
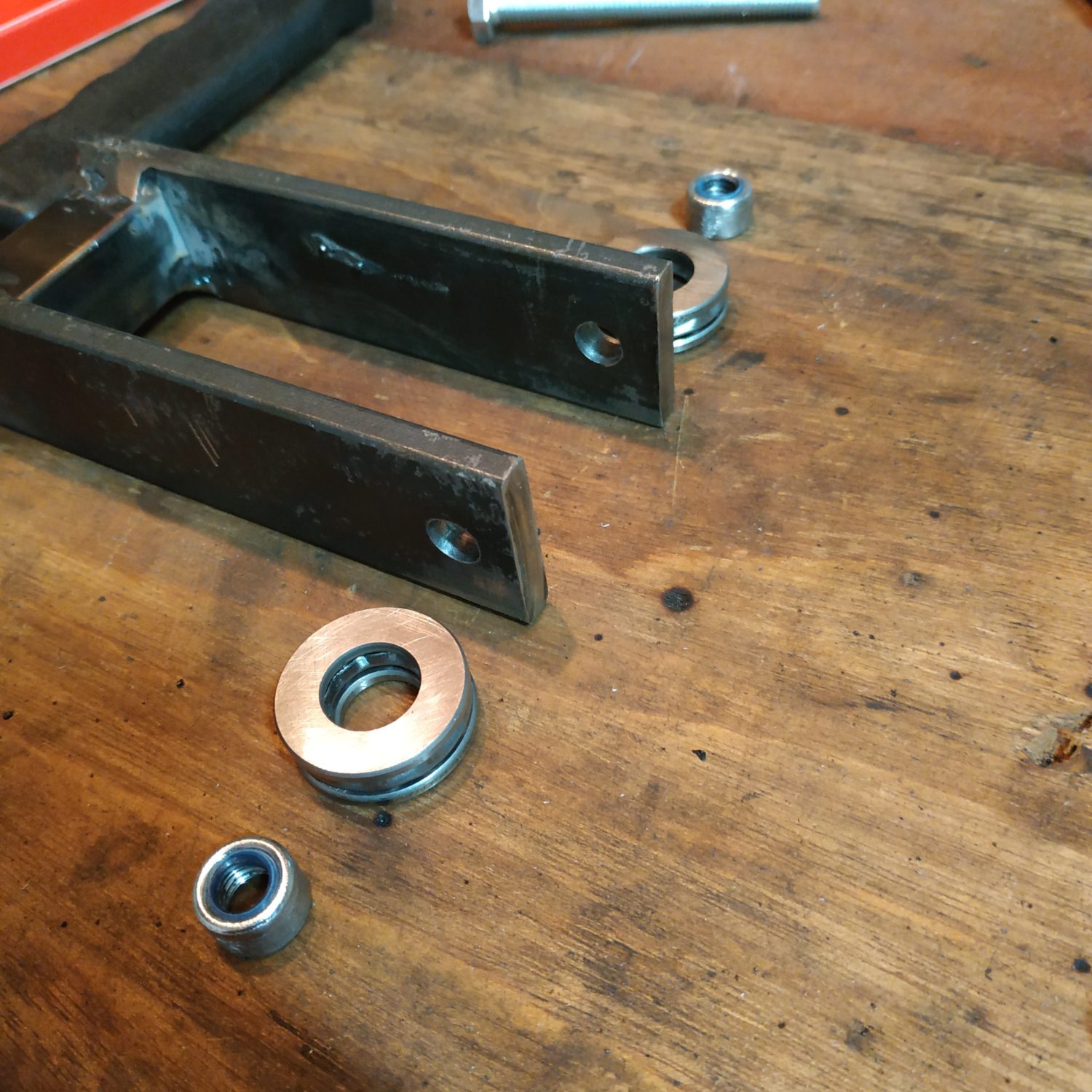
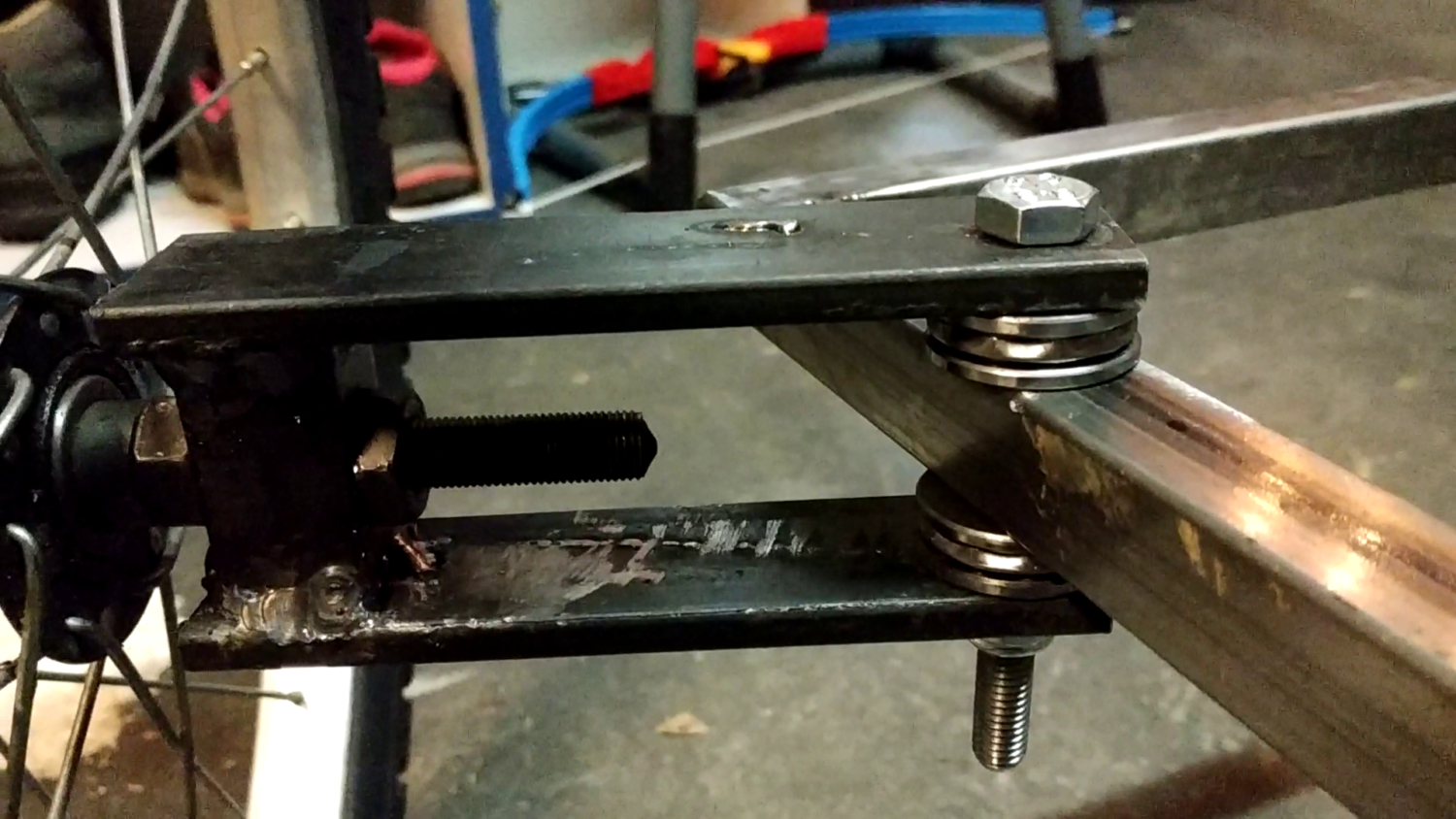
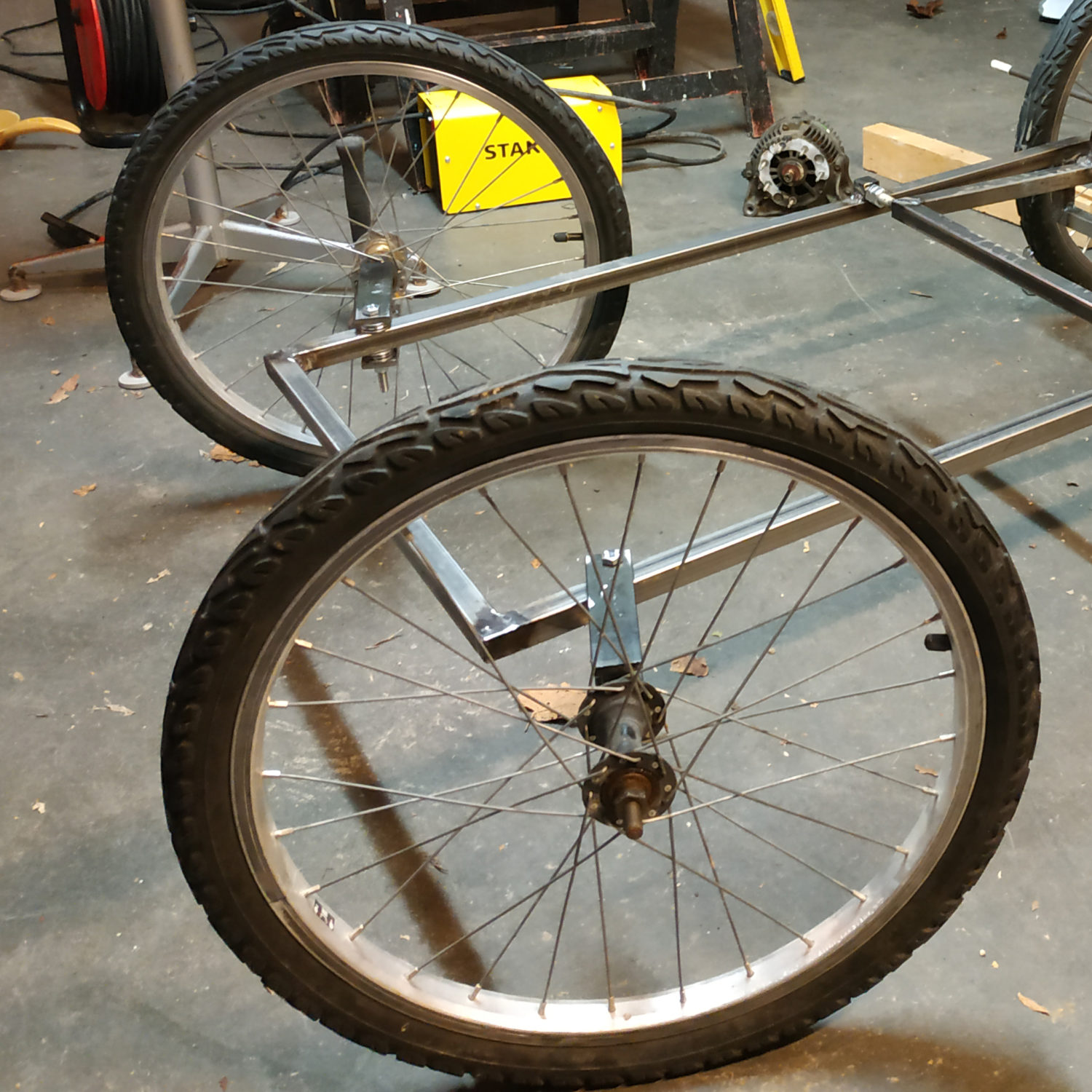
Le siège
Je m’attaque maintenant au siège. Je crée deux cadres en tube acier. Pas trop de photos pour cette étape. J’améliore mes soudures à 90° en découpant mes tubes à 45° grâce à un support de meuleuse, et en maintenant la soudure par des aimants. Je procède ensuite par pointillé le long de la coupe. Ainsi, je dépose petit à petit de la matière et je ne reste pas assez pour percer la matière. Le résultat est très solide. Je pense me débrouiller pour les soudures bord à bord et horizontale. On va pouvoir passer à plus compliqué.
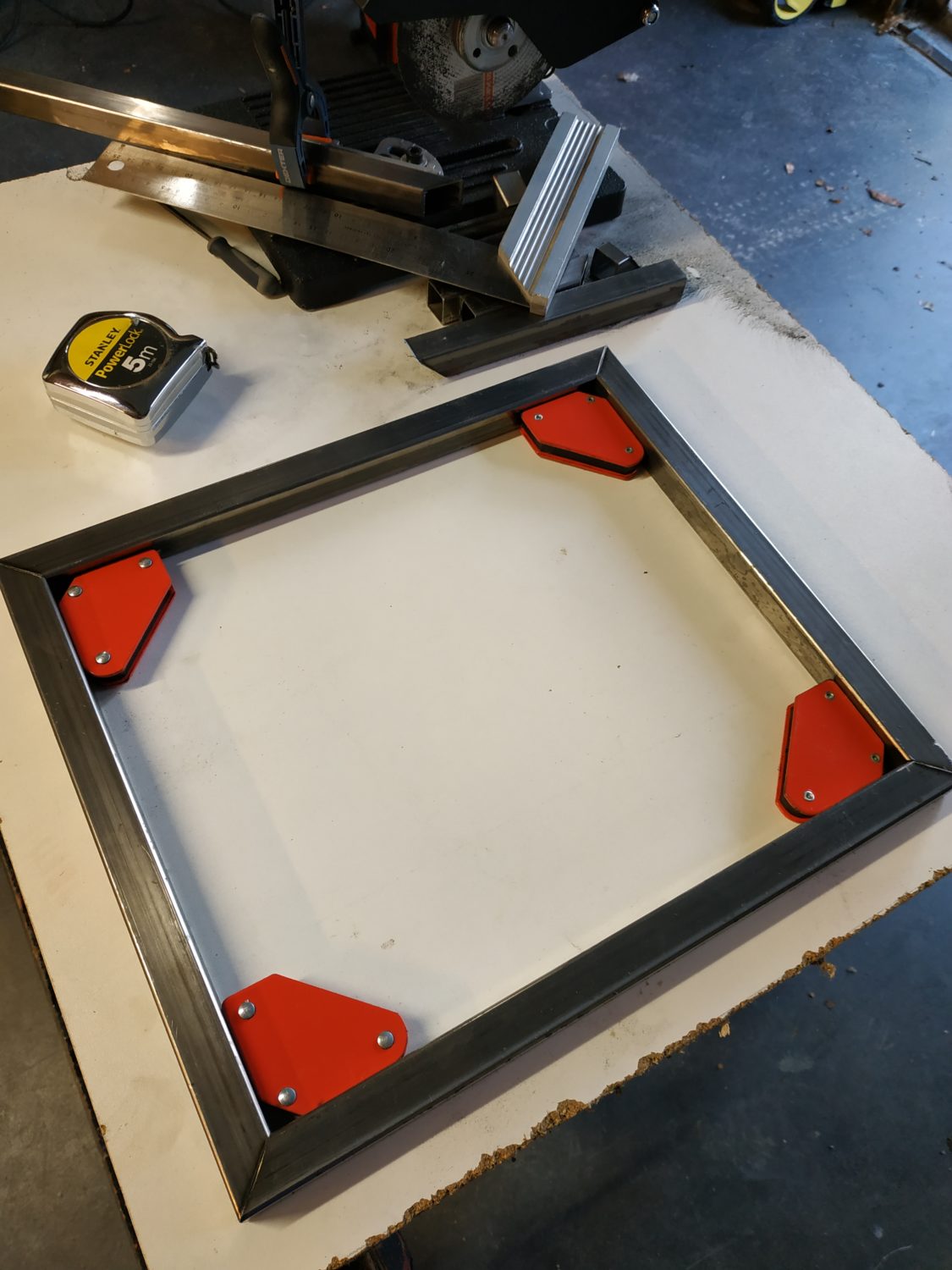
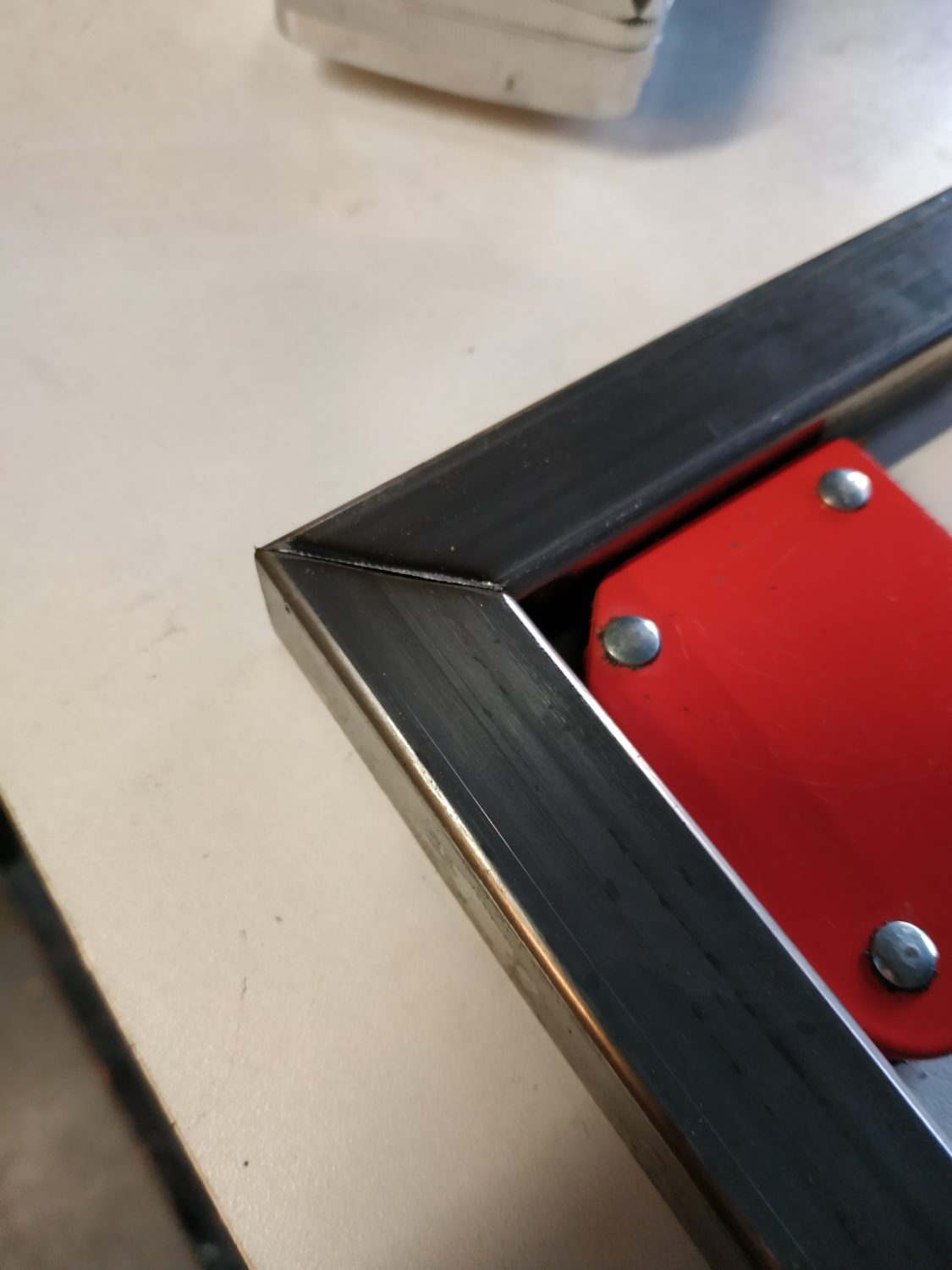
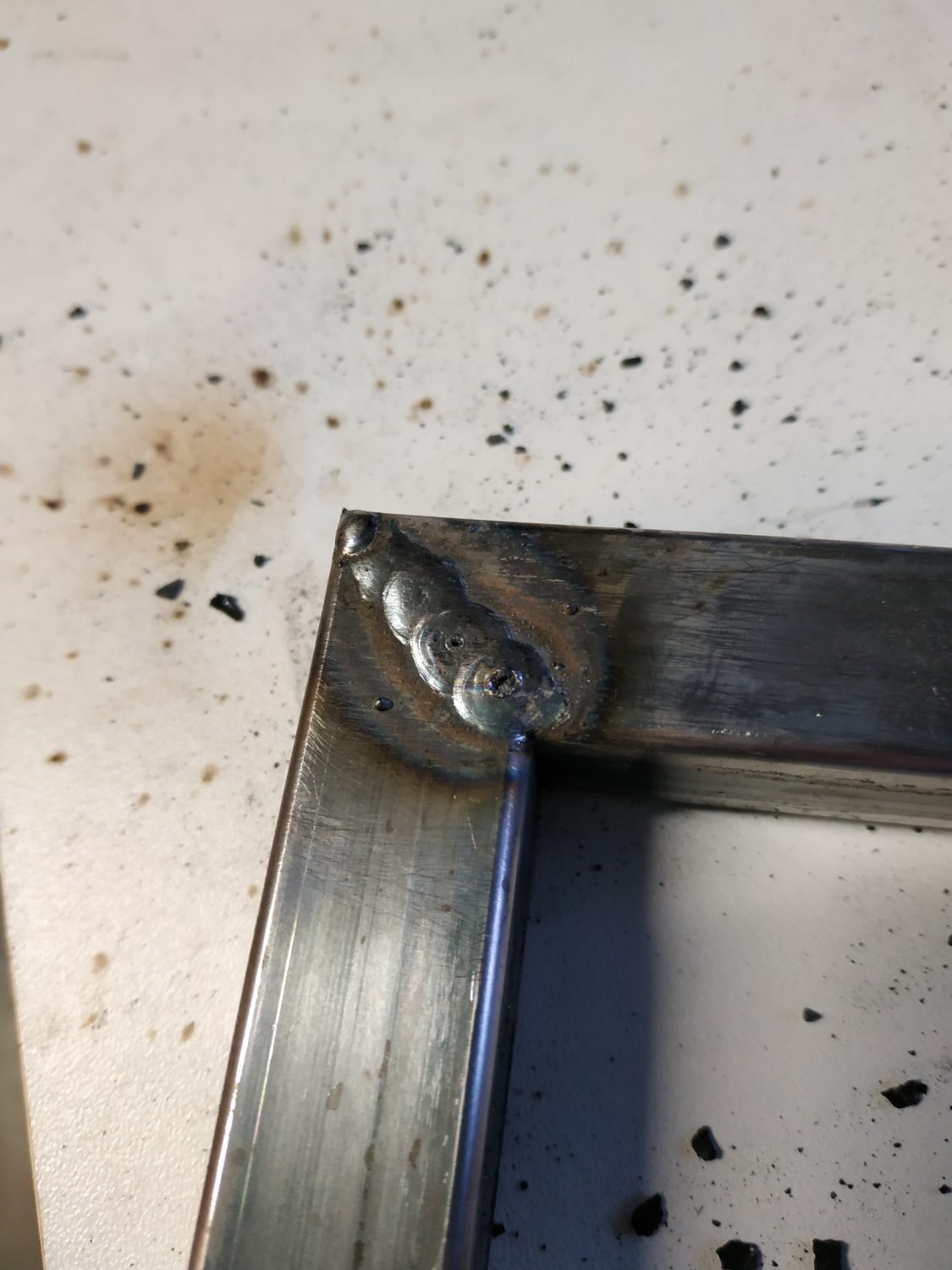
Je fixe le siège sur un axe pivotant sur le châssis, et un gros ressort + une barre de soutien me fait un siège confortable pour amortir les plus gros chocs.
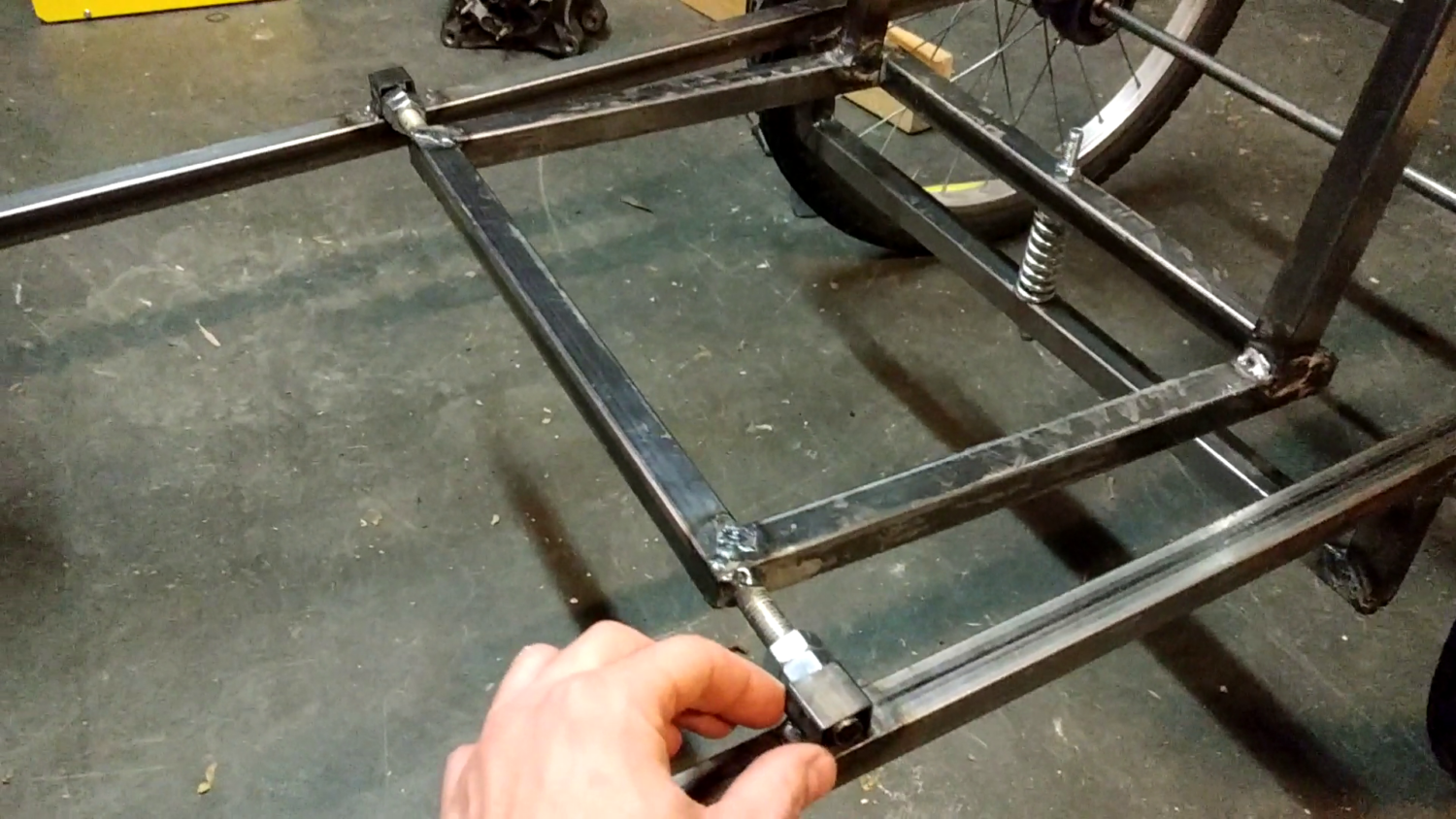
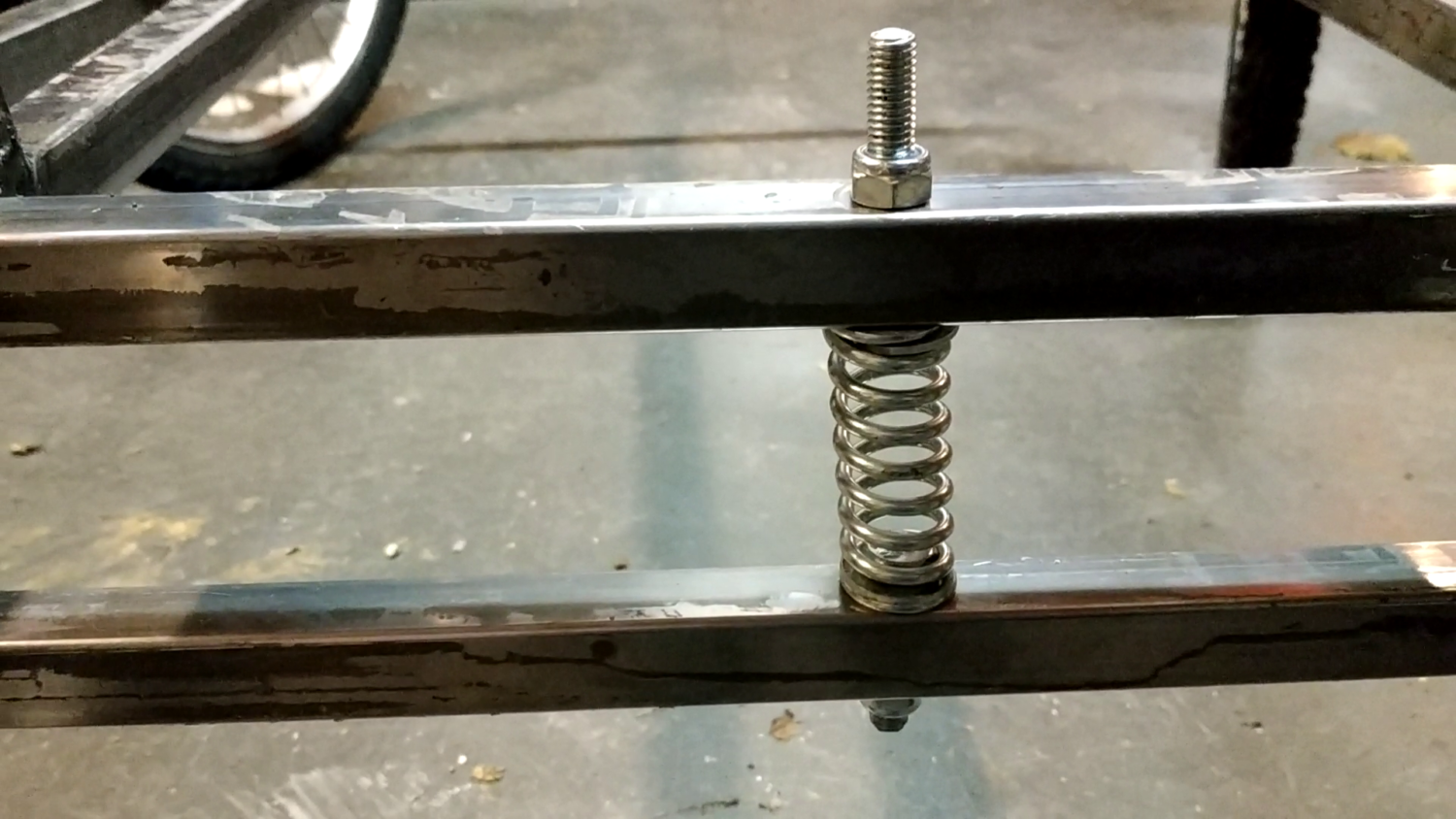
Et voici une vue d’ensemble !
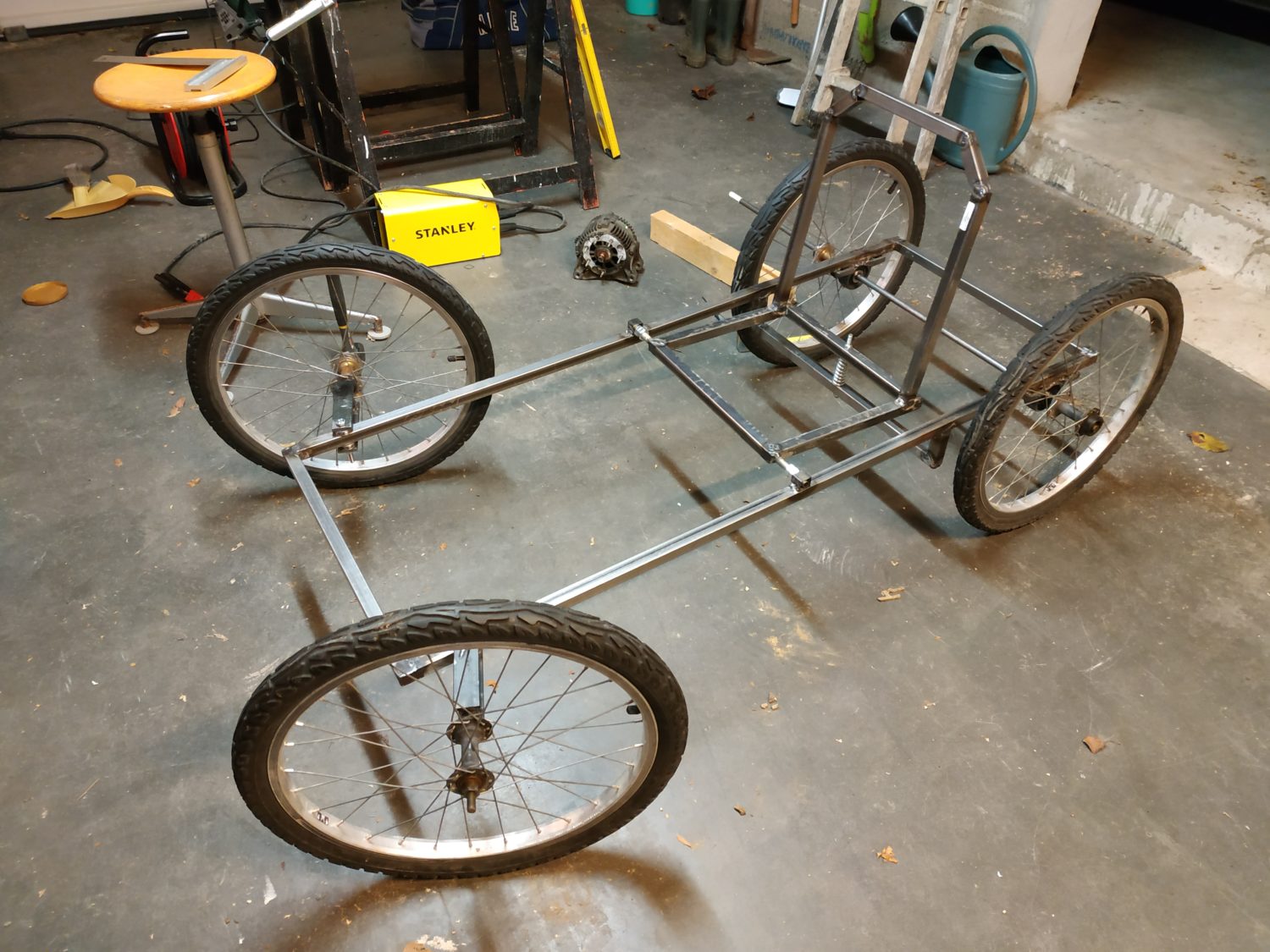
La direction
Maintenant que le châssis est construit, il faut rajouter une direction. Pour cela, je créé un cadre au dessus des genoux qui portera le volant. Le volant sera fixé le long d’une grande tige pleine en acier qui ira se loger à l’avant du châssis. Je soude un support pour recevoir l’extrémité de cette tige.
Sur cette tige, on fabrique une platine que l’on vient fixer et sur laquelle viendront se fixer les tiges orientant les roues. Ces tiges se terminent par de petites rotules qui permettent à l’ensemble de pousser/tirer les roues quelle que soit l’orientation du volant.
Pour éviter à la tige de direction de jouer d’avant en arrière dans son logement, je soude une rondelle à l’opposé du volant qui fait butée et empêche de la retirer. Le bas de la tige est fiché dans un bouchon pour tube carré en plastique que je perce au diamètre.
Le freinage (oups, ça freine fort)
Pour le freinage, j’opte pour un freinage à disque de vélo, dont je compte ramener le câble à une pédale sous les pieds. Le plus difficile est de fixer le disque bien perpendiculairement et concentriquement à l’axe de l’essieu. Je prépare des supports que je soude sur l’axe, mais comme je contrôle mal ma perpendicularité, je rattrape avec des rondelles en fixant le disque. Un crayon tenu devant le disque qui tourne me permet de marquer les zones qui se rapprochent de mon crayon et que je dois donc corriger. La concentricité est OK, mais de toute manière, l’étrier des plaquettes a une belle tolérance.
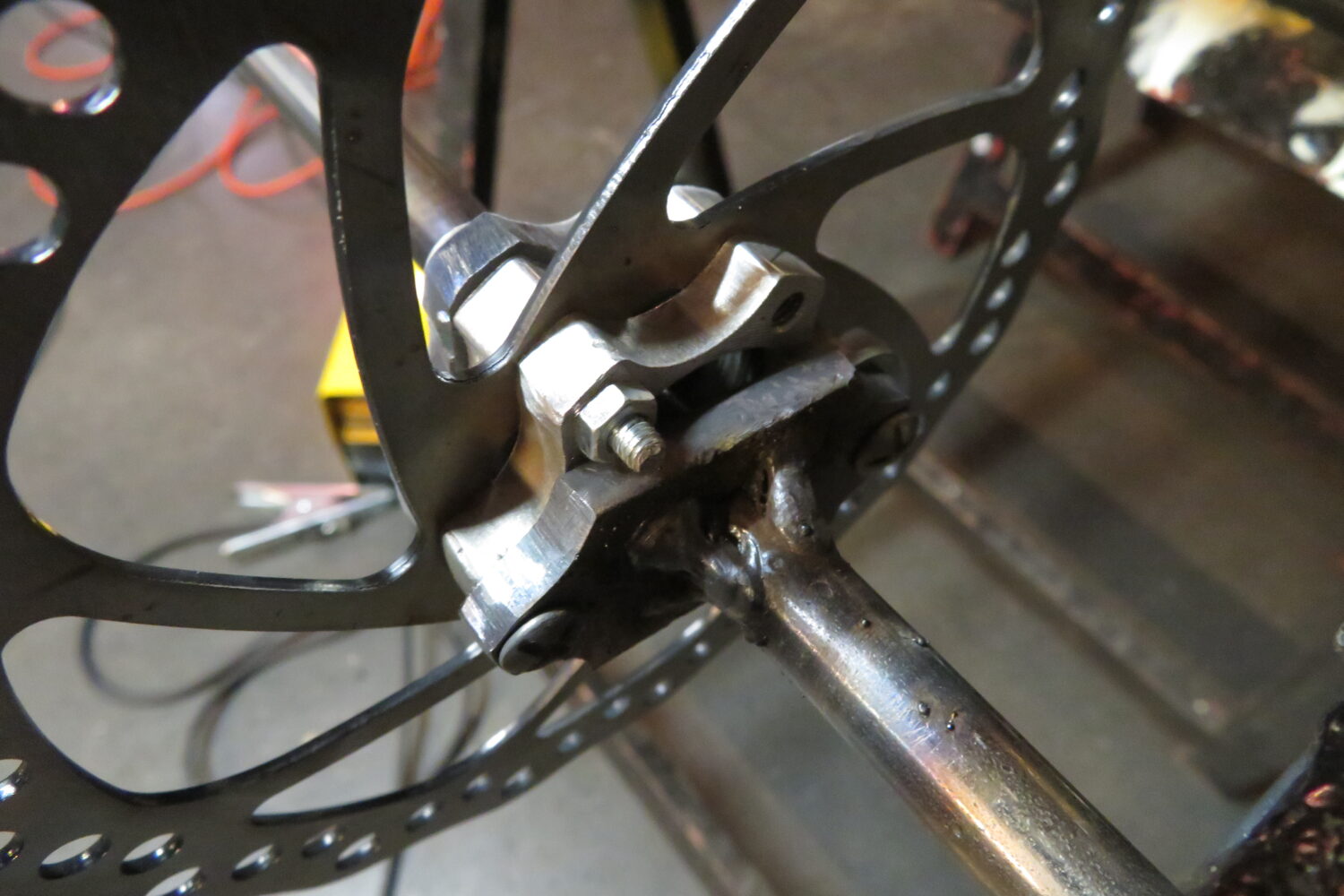
Je monte ensuite l’étrier sur une barre qui passe juste au dessus de l’essieu. Je peux régler en latéral, mais pas en hauteur, alors je m’applique à bien fixer l’ensemble à la bonne hauteur avant de le souder. Avant ce montage je fixe une série de pignon de VTT sur mon essieu, en gardant la « roue libre » de la cassette de pignons pour permettre de descendre sans le moteur: il n’y aura donc pas de marche arrière sur ce modèle..
Pour l’instant les roues sont goupillées sur l’essieu. Les premiers essais de descente et de freinage cisaillent la goupille instantanément. J’essaie plusieurs tige de différent métaux, rien n’y fait, alors je me décide à souder les roues à l’essieu. Je perd en démontabilité, mais c’est la seule solution à ma portée avec ces roues. Sur les karts, on trouve des essieux usinés d’une gorge qui reprennent un ergot de la roue, mais mes roues de vélo ne me laisse pas d’autres choix.
La motorisation
Je passe maintenant à la motorisation. Je prends mes conseils sur la chaîne de tchangly21 (ici: https://www.youtube.com/user/tchangly21/videos) qui rassemble beaucoup de contenus sur l’électrification de vélo, karts et autres véhicules, merci ! Je vais donc chercher un alternateur à la casse, et j’achète un contrôleur de moteur brushless, une batterie, une pédale d’accélération. L’alternateur subit une modification profonde pour pouvoir l’utiliser en moteur (démonstration ici: [Vidéo] Un alternateur converti en moteur brushless !).

Une fois le montage validé, je l’installe sur la voiture, via une petite démultiplication et une chaîne. L’alternateur est fixé sur une tige fileté sur un côté de manière à pouvoir le faire pivoter et régler ainsi la tension de la chaîne.
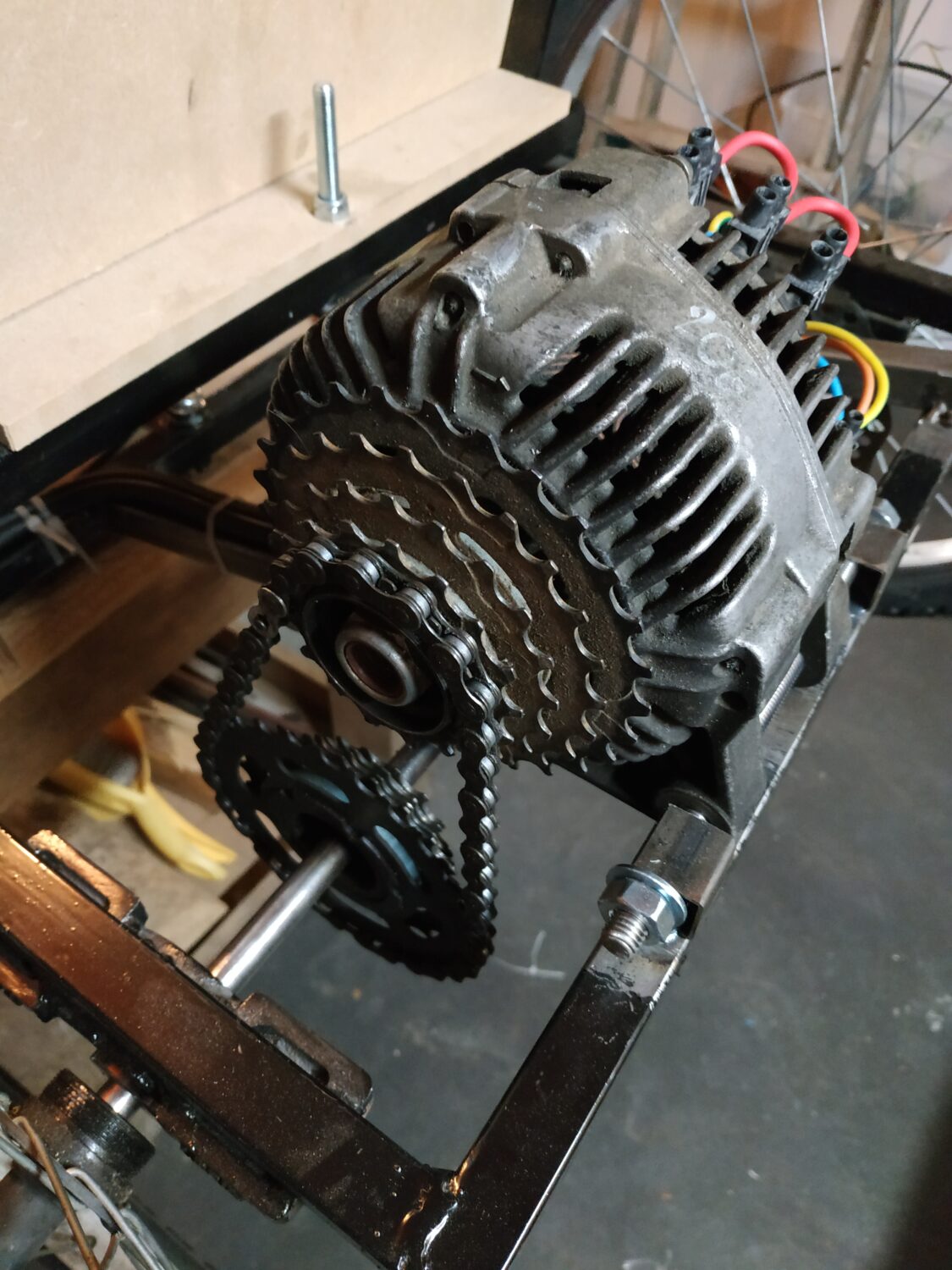
La démultiplication n’est pas suffisante: la voiture n’avance pas. Je suis donc obligé de faire tourner une troisième cassette de pignons qui permet de faire un rappel entre l’essieu et le moteur et ainsi d’augmenter la démultiplication. Je crée donc la forme de la caisse arrière et j’en profite pour installer ce rappel.
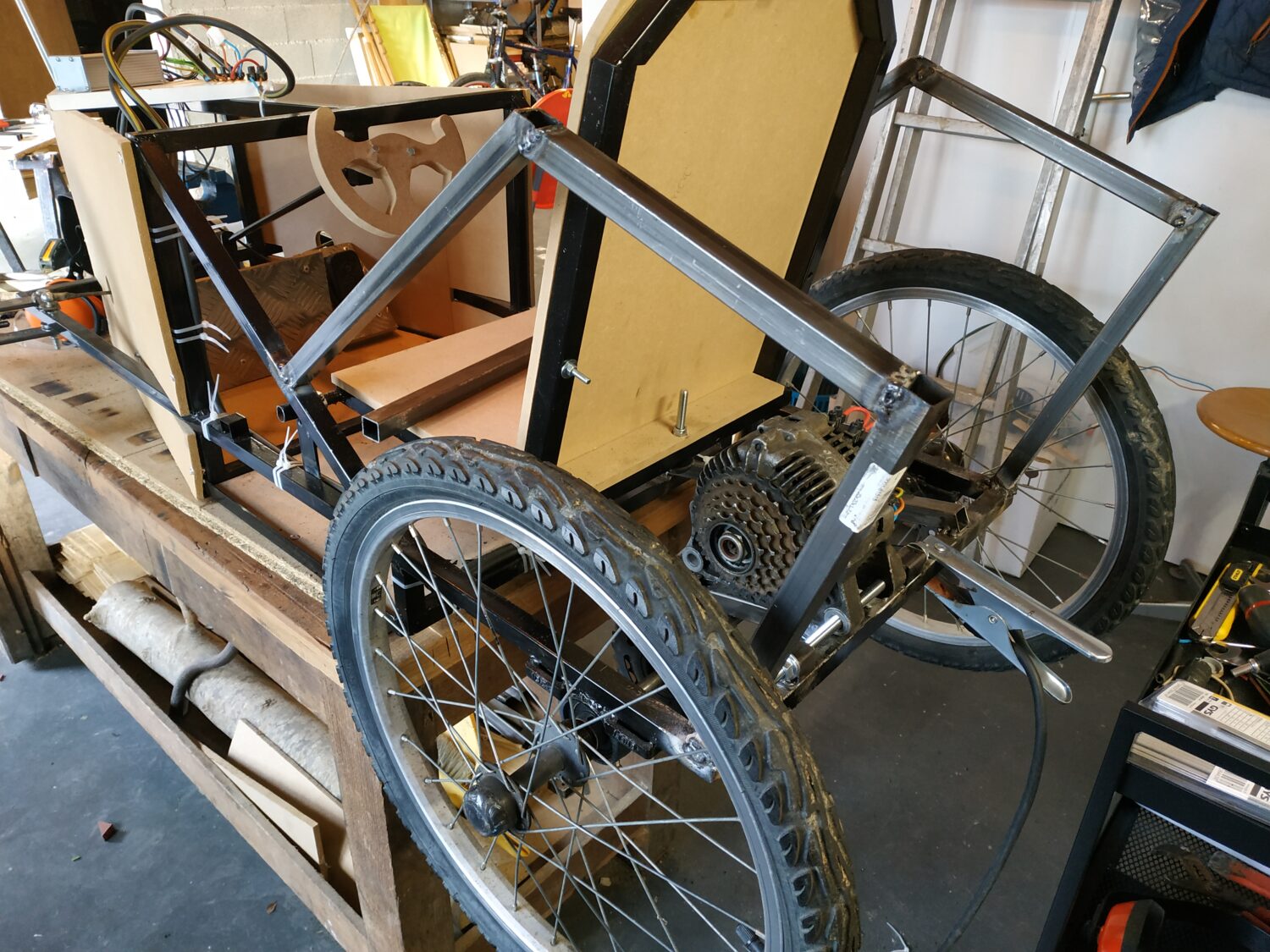
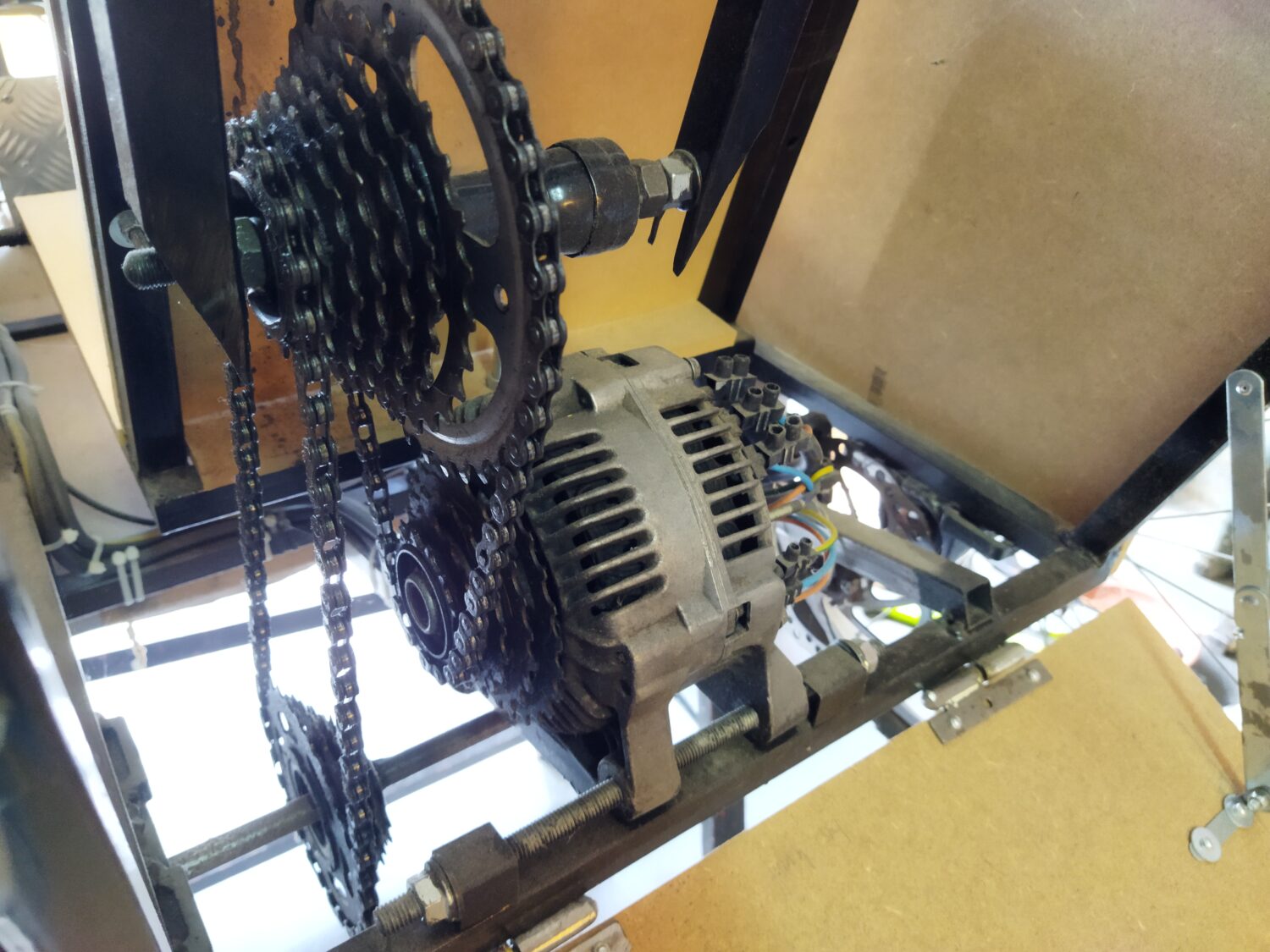
Pédales de frein et accélérateur
Je crée un pédalier robuste en MDF sur lequel je viens fixer la pédale d’accélérateur (à droite, histoire de prendre les bonnes habitudes), et je réserve une large plaque pour le frein. La plaque est mobile sur une charnière de porte pour garder de la robustesse: on veut pouvoir écraser le frein des deux pieds sans dommages.
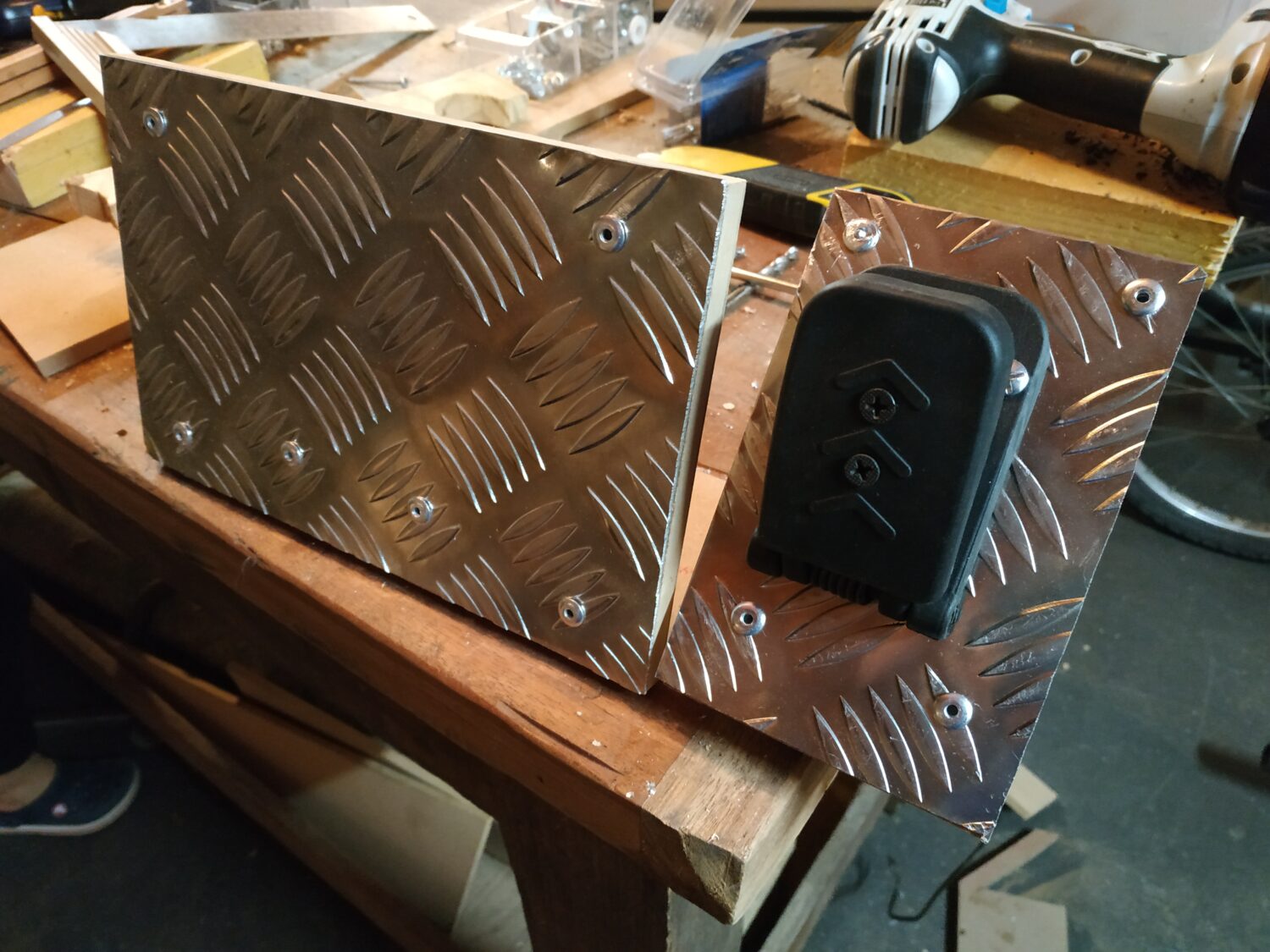
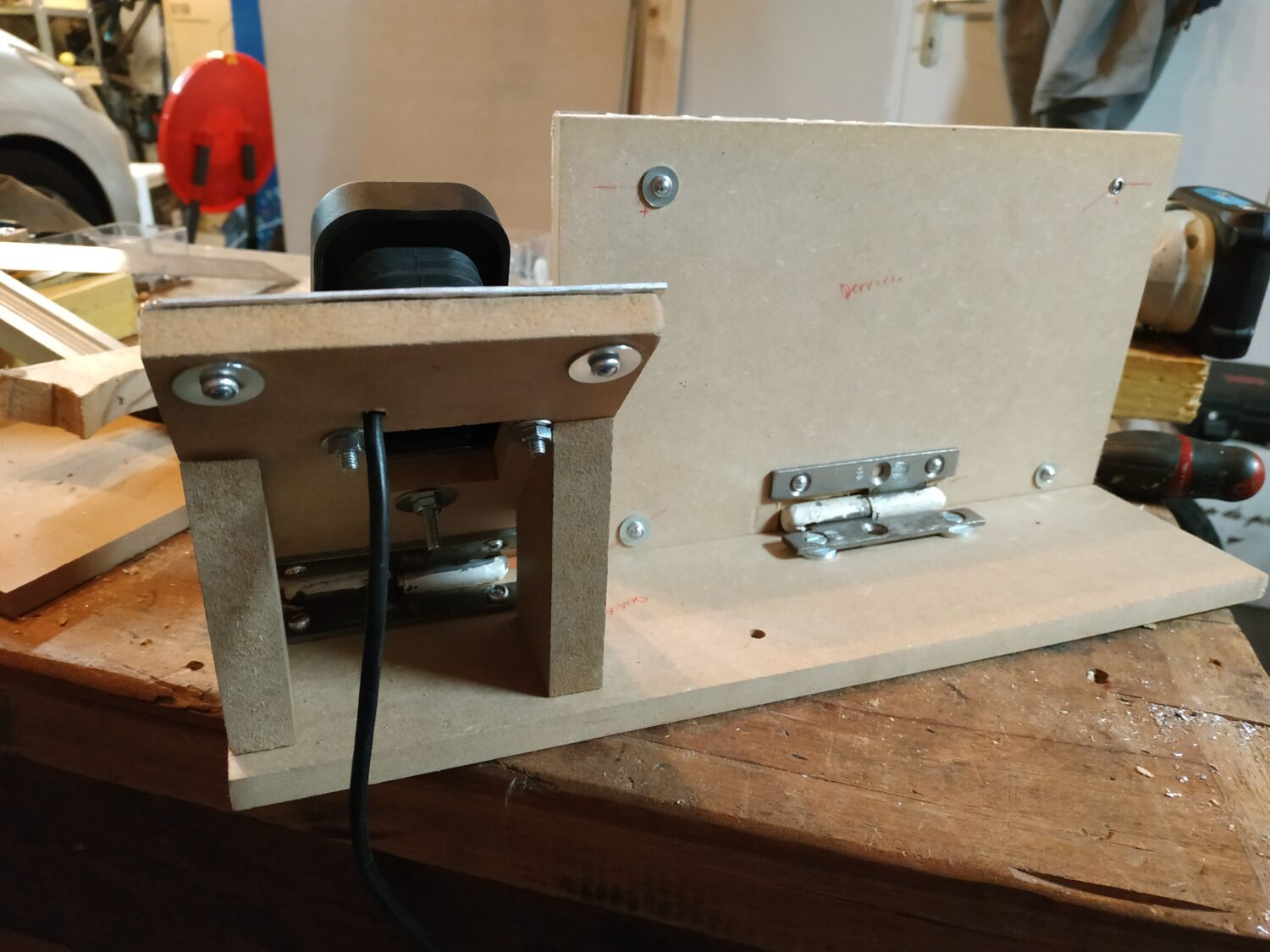
Habillage de la caisse
Pour l’habillage de la caisse, j’opte pour des panneaux de MDF rivetés sur les tubes de la voiture.
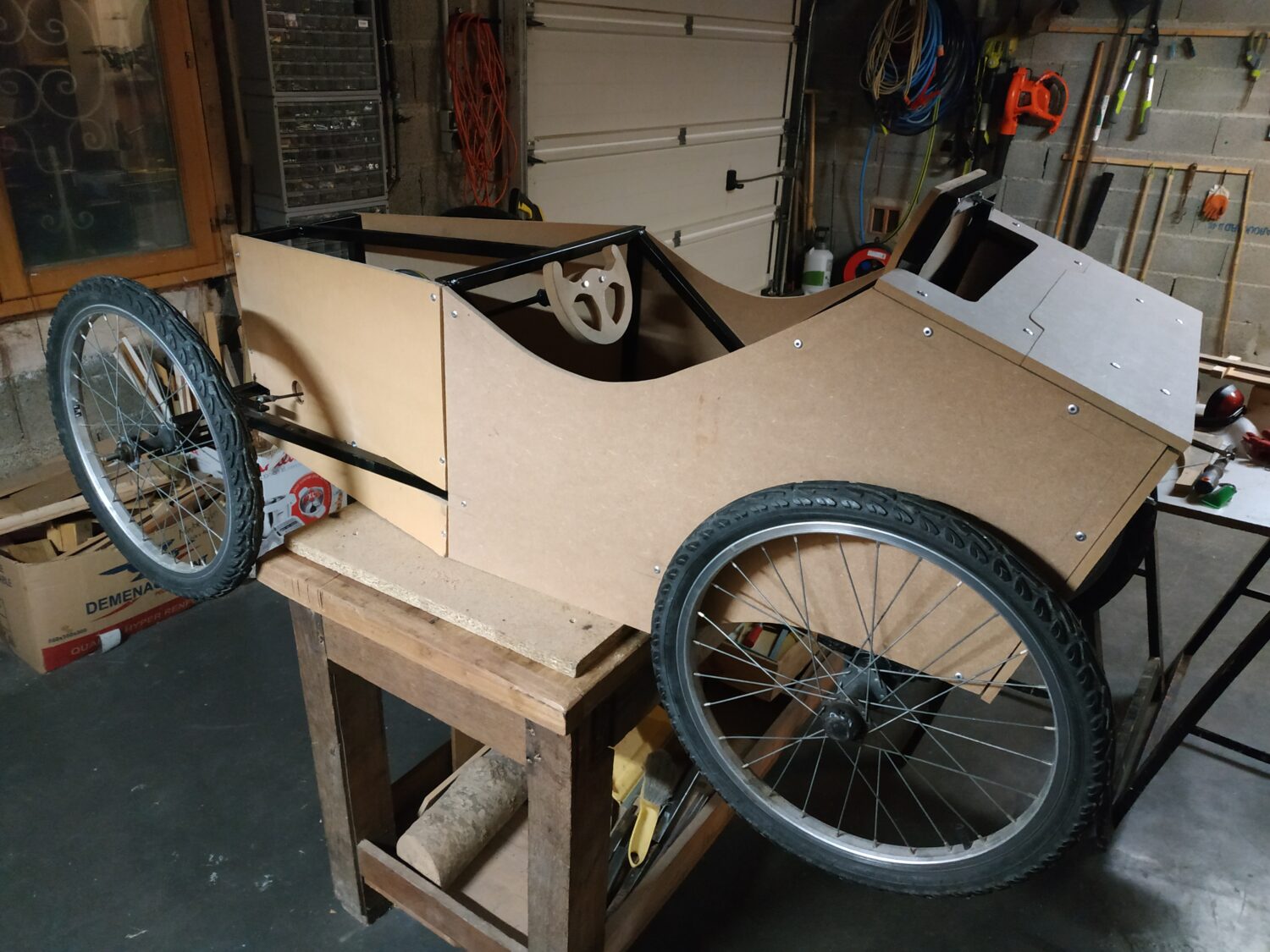
Pour la calandre, j’encolle trois épaisseurs de panneaux que je découpe et que je ponce sur la voiture directement pour donner le « look » attendu. Au passage, je crée une petite étagère sur laquelle je viens fixer le contrôleur et où je fais arriver les câbles qui alimentent le moteur à l’arrière.
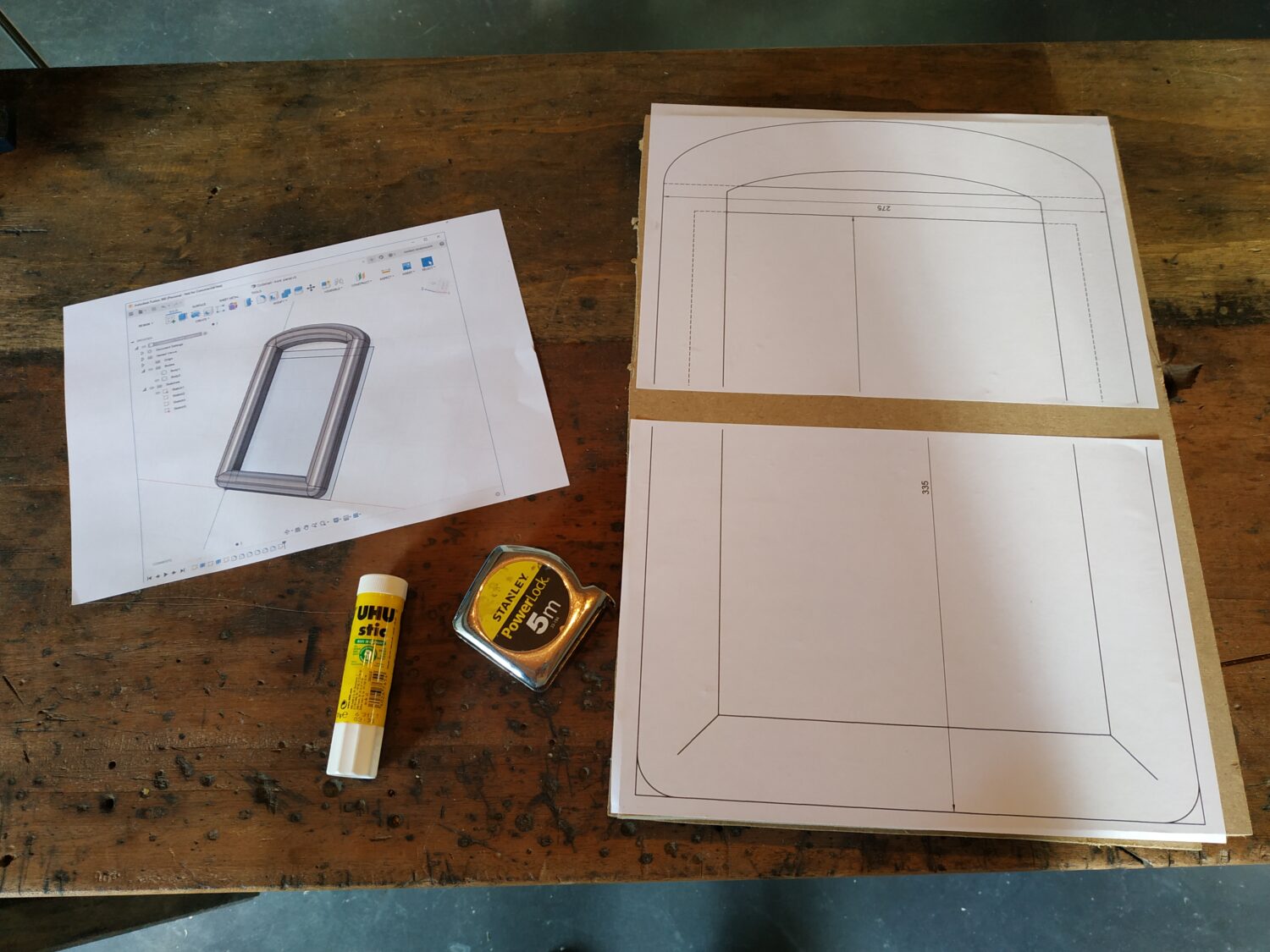
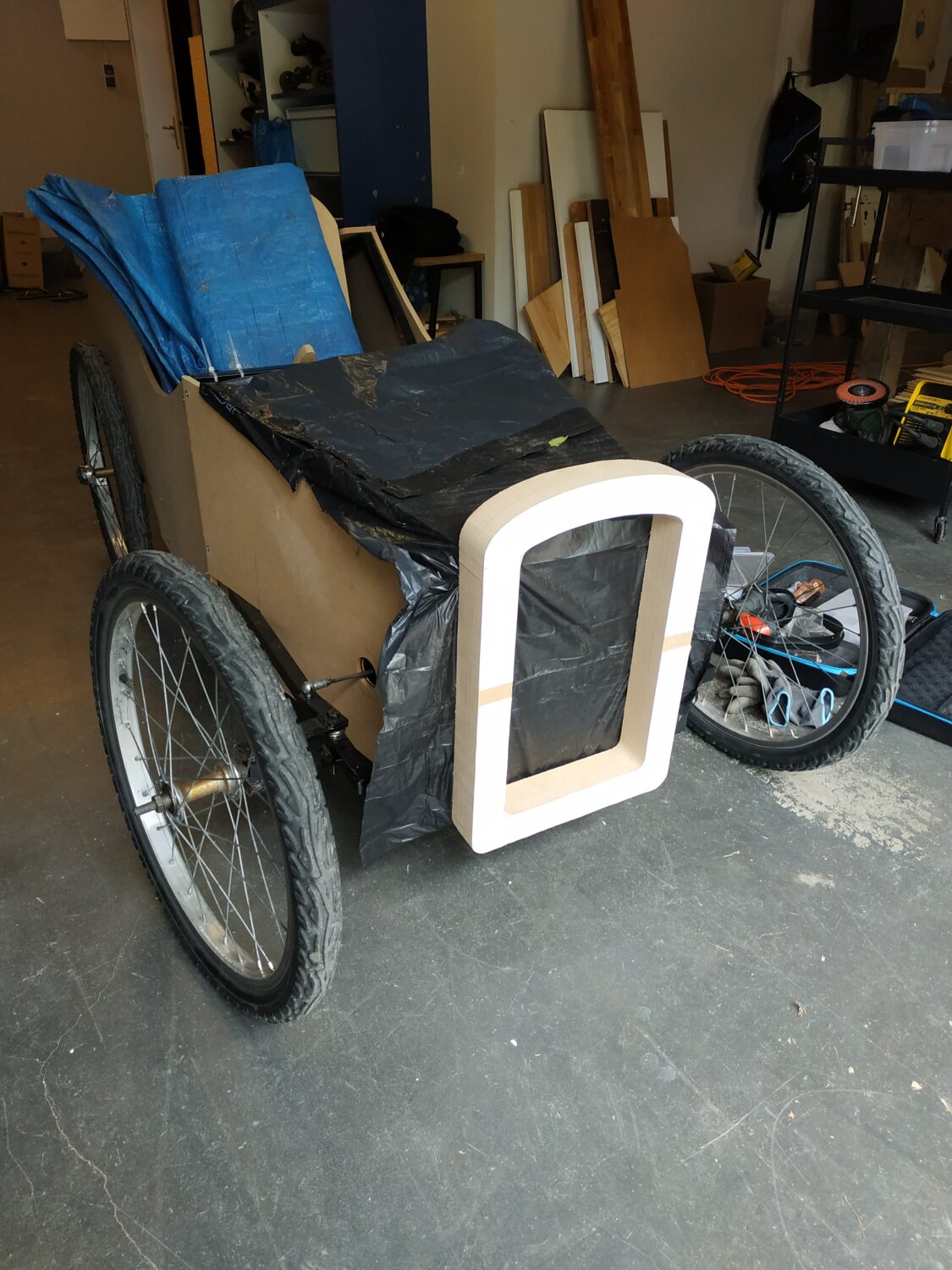
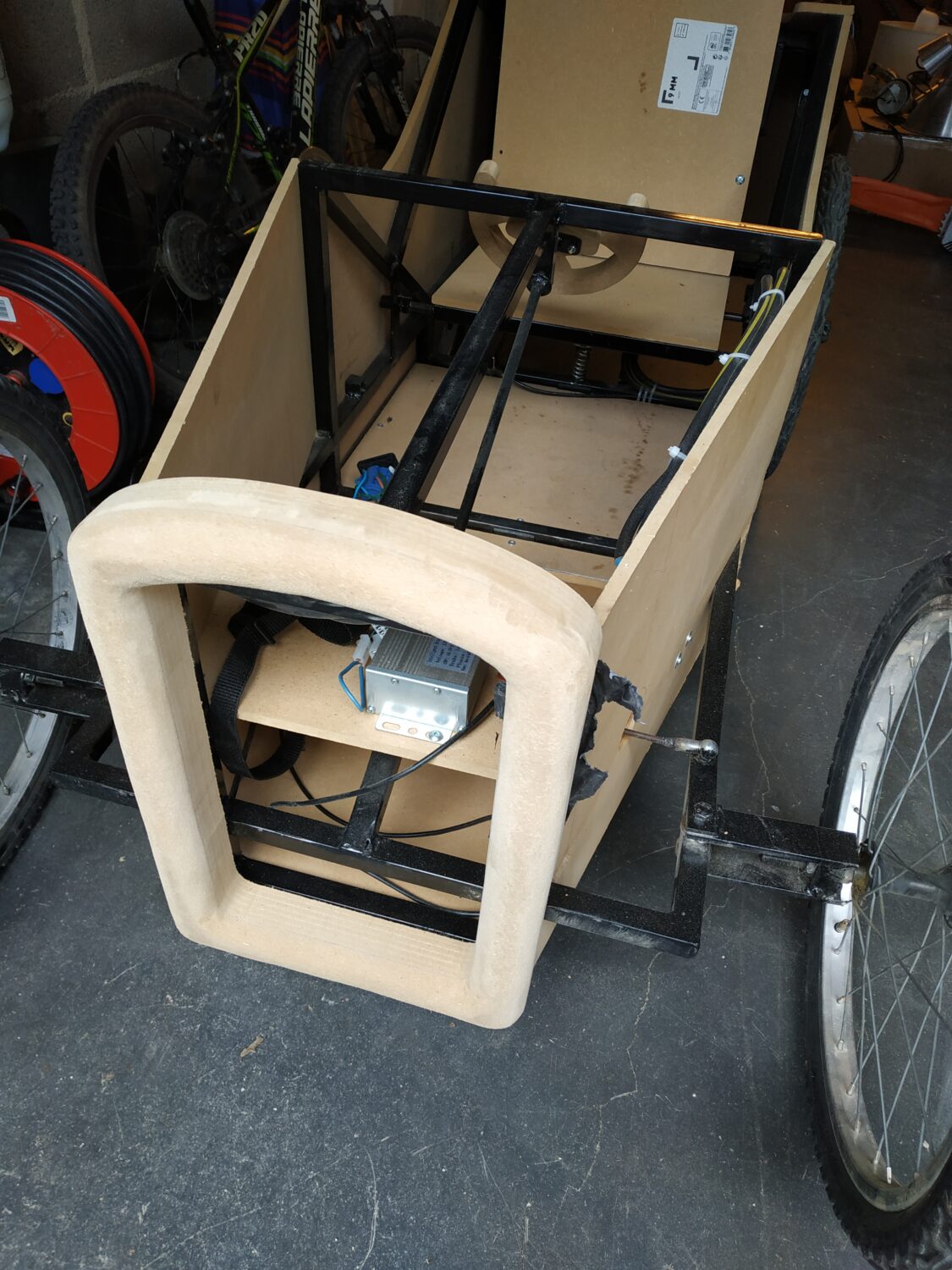
Je réalise le capot avec une base de MDF et 4 formes sur lesquelles je viens forcer une fine lame de MDF (de celle que l’on trouve au fond des placards), humidifiée pour prendre plus facilement la forme.
A suivre !